1000 kilometer range for an electric vehicle?
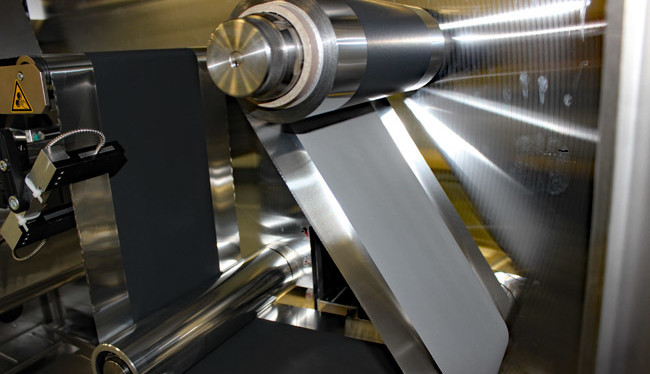
When it comes to purely electric vehicles, poor range is still the number one reason why they are not more popular. This all boils down to the relatively low energy density of batteries compared to other fuels. A relevant parameter in this context is the space requirement of the batteries. New technology from Fraunhofer IKTS uses large-area stacked cells one above the other. This technology could produce cars with a range of 1,000 kilometers...
When it comes to purely electric vehicles, poor range is still the number one reason why they are not more popular. This all boils down to the relatively low energy density of batteries compared to other fuels. A relevant parameter in this context is the space requirement of the batteries. New technology from Fraunhofer IKTS uses large-area stacked cells one above the other. This technology could produce cars with a range of 1,000 kilometers.
The battery packs used in today’s electric vehicles, such as the Tesla, are made up of thousands of individual standard cells, each in their own (generally cylindrical) case. The housing, monitoring and cabling of so many cells take up more than 50% of the total space of the battery compartment in the vehicle. This means that the available space is not optimally used and electrical losses are incurred in the interconnections.
The Fraunhofer Institute for Ceramic Technologies has partnered with Systems IKTS in Dresden to produce new technology under the brand name EMBATT which transfers the so-called "bipolar principle" used for fuel cells to lithium cell technology. The cells are stacked directly on top of one another. All the additional space needed for the cell housing and interconnections are thus no longer required, producing a much improved energy density. This equates to a smaller battery compartment to give the same range or the same size compartment giving extended range.
The EMBATT bipolar battery consists of stacked cells, in which the current collector of the negative electrode of one cell is in contact with the positive electrode of the next cell. Thus, two electrochemical cells connected in series share one current collector – one side of the bipolar electrode serves as the anode in one cell and the other side as the cathode in the next cell.
This multi-cell configuration produces extremely low interconnection resistance, good heat conduction, fewer individual cells and significantly reduced monitoring complexity. The drawback is that individual cells cannot swapped-out, only entire battery packs. This disadvantage is mitigated by the fact that the car battery would not consist of a monolithic block, but built up from several blocks to give the required cell count and total voltage. Initial tests in a vehicle are scheduled for 2020.
The battery packs used in today’s electric vehicles, such as the Tesla, are made up of thousands of individual standard cells, each in their own (generally cylindrical) case. The housing, monitoring and cabling of so many cells take up more than 50% of the total space of the battery compartment in the vehicle. This means that the available space is not optimally used and electrical losses are incurred in the interconnections.
The Fraunhofer Institute for Ceramic Technologies has partnered with Systems IKTS in Dresden to produce new technology under the brand name EMBATT which transfers the so-called "bipolar principle" used for fuel cells to lithium cell technology. The cells are stacked directly on top of one another. All the additional space needed for the cell housing and interconnections are thus no longer required, producing a much improved energy density. This equates to a smaller battery compartment to give the same range or the same size compartment giving extended range.
The EMBATT bipolar battery consists of stacked cells, in which the current collector of the negative electrode of one cell is in contact with the positive electrode of the next cell. Thus, two electrochemical cells connected in series share one current collector – one side of the bipolar electrode serves as the anode in one cell and the other side as the cathode in the next cell.
This multi-cell configuration produces extremely low interconnection resistance, good heat conduction, fewer individual cells and significantly reduced monitoring complexity. The drawback is that individual cells cannot swapped-out, only entire battery packs. This disadvantage is mitigated by the fact that the car battery would not consist of a monolithic block, but built up from several blocks to give the required cell count and total voltage. Initial tests in a vehicle are scheduled for 2020.