New Rotary Encoder
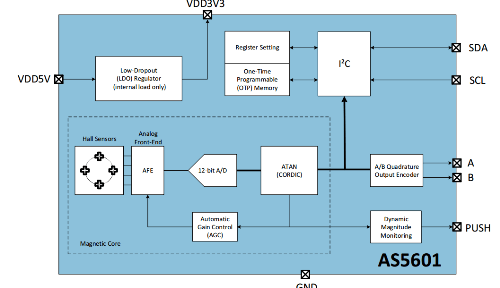
The Company AMS AG has introduced the non-contact AS5601 Hall-based rotary magnetic position encoding chip. It works by sensing changes in the magnetic field components perpendicular to the surface of the chip and converts field changes into voltages to produce incremental A/B outputs and absolute...
The Company AMS AG has introduced the non-contact AS5601 Hall-based rotary magnetic position encoding chip. It works by sensing changes in the magnetic field components perpendicular to the surface of the chip and converts field changes into voltages to produce incremental A/B outputs and absolute position information that can be read over an I²C bus. Analog signals from the built-in Hall sensors are amplified and filtered before conversion to binary values. A hardwired CORDIC block (Coordinate Rotation Digital Computer) calculates the angle and magnitude of the magnetic field vector. Magnetic field intensity is used by the automatic gain control (AGC) to adjust the amplification level which compensates for temperature and magnetic field variations.
Internal logic uses the angle value provided by the CORDIC algorithm to generate the incremental quadrature signals A and B. The magnitude and AGC value is dynamically monitored and generates a PUSH output to indicate a control-knob press when a sudden change in the distance to the magnet is detected. Slow changes are ignored to make the chip tolerant of temperature variation and magnet degradation.
The AS5601 uses an I²C interface to program an on-chip one-time programmable (OTP) memory. This interface can be used to define a reference zero point of the rotation. The typical airgap between the rotating magnet and chip surface is between 0.5 and 3 mm, depending on the magnet used. The chip can be powered from 5 V or 3.3 V.