Laser sparks revolution in internal combustion engines
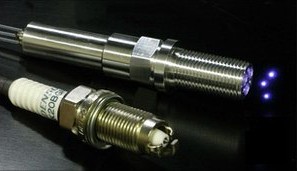
For more than 150 years, spark plugs have powered internal combustion engines. Automakers are now one step closer to being able to replace this long-standing technology with laser igniters, which will enable cleaner, more efficient, and more economical vehicles.
In the past, lasers strong enough to ignite an engine’s air-fuel mixtures were too large to fit under an automobile's hood. At this year's Conference on Lasers and Electro Optics (CLEO: 2011), held in Baltimore May 1 - 6, researchers from
|
|
Equally significant, the new laser system is made from ceramics, and could be produced inexpensively in large volumes, according to one of the presentation's authors, Takunori Taira of
According to Taira, conventional spark plugs pose a barrier to improving fuel economy and reducing emissions of nitrogen oxides (NOx), a key component of smog.
Spark plugs work by sending small, high-voltage electrical sparks across a gap between two metal electrodes. The spark ignites the air-fuel mixture in the engine's cylinder — producing a controlled explosion that forces the piston down to the bottom of the cylinder, generating the horsepower needed to move the vehicle.
Engines make NOx as a byproduct of combustion. If engines ran leaner – burnt more air and less fuel – they would produce significantly smaller NOx emissions.
Spark plugs can ignite leaner fuel mixtures, but only by increasing spark energy. Unfortunately, these high voltages erode spark plug electrodes so fast, the solution is not economical. By contrast, lasers, which ignite the air-fuel mixture with concentrated optical energy, have no electrodes and are not affected.
Lasers also improve efficiency. Conventional spark plugs sit on top of the cylinder and only ignite the air-fuel mixture close to them. The relatively cold metal of nearby electrodes and cylinder walls absorbs heat from the explosion, quenching the flame front just as it starts to expand.
Lasers can focus their beams directly into the center of the mixture. Without quenching, the flame front expands more symmetrically and up to three times faster than those produced by spark plugs. Equally important, lasers inject their energy within nanoseconds, compared with milliseconds for spark plugs.
Lasers promise less pollution and greater fuel efficiency, but making small, powerful lasers has, until now, proven hard. To ignite combustion, a laser must focus light to approximately 100 gigawatts per square centimeter with short pulses of more than 10 millijoules each.
Taira’s research team overcame this problem by making composite lasers from ceramic powders. The team heats the powders to fuse them into optically transparent solids and embeds metal ions in them to tune their properties.
Ceramics are easier to tune optically than conventional crystals. They are also much stronger, more durable, and thermally conductive, so they can dissipate the heat from an engine without breaking down.
Taira’s team built its laser from two yttrium-aluminum-gallium (YAG) segments, one doped with neodymium, the other with chromium. They bonded the two sections together to form a powerful laser only
The composite generates two laser beams that can ignite fuel in two separate locations at the same time. This would produce a flame wall that grows faster and more uniformly than one lit by a single laser. The laser is not strong enough to light the leanest fuel mixtures with a single pulse. By using several 800-picosecond-long pulses, however, they can inject enough energy to ignite the mixture completely.
A commercial automotive engine will require 60 Hz (or pulse trains per second), Taira says. He has already tested the new dual-beam laser at 100 Hz. The team is also at work on a three-beam laser that will enable even faster and more uniform combustion.
The laser-ignition system, although highly promising, is not yet being installed into actual automobiles made in a factory. Taira’s team is, however, working with a large spark-plug company and with DENSO Corporation, a member of the Toyota Group. This work is supported by the Japan Science and Technical Agency (JST).
Photo courtesy Takunori Taira, National Institutes of Natural Sciences,