Minimizing Hardware with Smart Software: Zooming in on the Technology at InnoFaith
In May, I met Walter Arkesteijn, not only as an enthusiastic entrepreneur but also as an Elektor aficionado and an inspirer. High time, I figured, to enter the lab of the Eindhoven-based company InnoFaith Beauty Sciences to discover how their high-end equipment for skin analysis is created.
To understand the way the hardware and software developers at Innofaith work, it is useful to look at the company philosophy. That is not difficult to do at the “Esp” high-tech industrial zone in Eindhoven, The Netherlands. As already shown in the previous article, creativity and collaboration are core factors in the company and those skills are applied broadly and consistently at all levels. For example, almost all staff members at InnoFaith give input for the “look and feel” of the app that goes with their main product, the Observ 520x skin analyzer. As Walter Arkesteijn pointed out, everyone is mindful they are creating a technically complex product for, essentially, non-technical users who, in turn, work with clients in a clinic or other location where skin analysis is conducted.
Despite the large amount of internal and external input around the product, it naturally happens that the technicians seek help for a problem or get stuck in a software or hardware development. Arkesteijn then starts “reflecting” with them, a process in which short stop moments and loops are inserted in the reported progress until a successful exit is found. Sometimes, this results in a totally new (partial) product or (software) module that is put on the shelf for later use. These conversations are therefore stimulating rather than critical, which technicians tend to appreciate among themselves. The communication lines at InnoFaith are very short.
Stepping into the InnoFaith Lab
Siedse Buijs, Senior Electronics Engineer at InnoFaith, is a multidisciplinary electronics engineer. For product development, he mainly collaborates with Senior Engineer Han van Triest and Software Developers Rowan Dings and Sander de Laat.
Visiting the InnoFaith electronics development space, I can guess the outcome of the Software-against-Hardware match that Elektor readers are also familiar with: 1-0. Or maybe 2-1, but in any case in favor of the bits, bytes, and C++ over transistors and solder fumes. At InnoFaith, the technical adage is: to simplify your hardware to the limit and let the software and especially the microcontroller do the work.
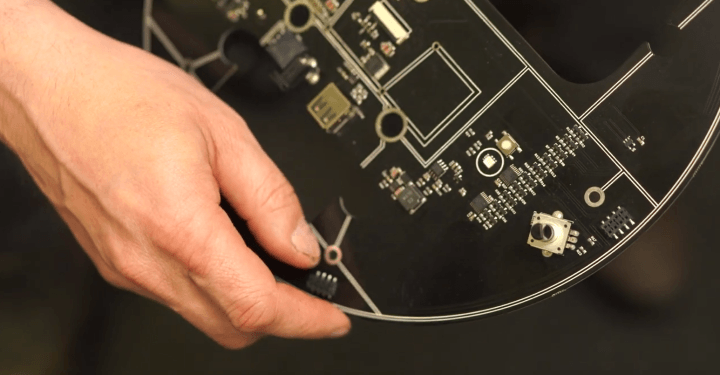
LED in a chain to be turned on and off individually.
A nice example is the control of a number of UV LEDs mounted in a ring form. Siedse shows the PCB of an early prototype (Figure 1) and explains that you can “... tie all LEDs in series nice and easy and make them light up evenly under constant-current control, but what if you want to turn off 1 or 2 LEDs in such a chain to get a particular light pattern rather than a circle?” The answer is on the circular circuit board: not a component grave with large heatsinks but a field of “cool” SMD MOSFETs that can effectively “kill” one LED each under software control without reducing the brightness of the others.
The concept of “communication” in the lab is not limited to electronic elements, buses, and the like — there is plenty of sparring, discussion, and brain-picking in a lively technical forum in which Siedse and his direct colleagues consult and help many external heads on a daily basis as pictured in Figure 2.
The Observ 520x from InnoFaith
Han van Triest passionately explains the working principle of the Observ 520x, the firm’s flagship product sold worldwide under the Sylton brand name. Six software-controlled UV LEDs act as point sources, each illuminating a precisely shaped reflector dish (Figure 3). That saucer shape is a fine piece of optics and physics. The customer’s face can be properly illuminated with diffused light as the sources are fully configurable. For the measurement, the customer must hold the head steady at an optimal distance from the sensor.
The subjects of optics and electronics blend nicely here.
For this purpose, a chin rest and an interactive “parking aid” that indicates to the patient/client “up please” or “down please” with a dash on a super small display (Figure 4). The exact distance between camera and face is determined with an ultrasonic measurement.
The image of the face is recorded by an Apple iPad camera known for its reliability and stable image output just for this application. Meanwhile, the skin specialist sees both the face and the bar display on the app, where he or she can also adjust the light distribution and intensity or request a certain action from the patient. Usually, a tablet is used on the specialist/consultant side. Incidentally, the UV dose to the patient is well within generally accepted standards as well as accurately tracked.
The images saved via the app at various settings are stored for analysis, later or onsite, by a skin specialist or cosmetic consultant. Also, the images captured before and after a skin treatment can be easily compared.
There is an absolutely minimal amount of electronics (“hardware”) in the Observ 520x; most of it actually serves to communicate with the app via Bluetooth and the outside world via Wi-Fi.
Modules = No Hassle
Among InnoFaith’s developers, the “minimum hardware” rationale also applies to elements that are better bought as modules than developed in-house. Buying (prudently) and applying tried and tested things like a power adapter, a Bluetooth, or Wi-Fi module (Figure 5) largely liberates you from problems with certifications, import regulations, and border checks. It also frees up time for the really interesting work: creating smart software to communicate with those modules. Fast, safe, and super dependable — for non-technical people!
work of a complex device like the Observ 520x skin analyzer.
Sure, a variacAs the only “vintage” element among all the miniature electronics, microcontroller systems, and state-of-the-art measurement equipment in InnoFaith’s development lab, the light brown, totally old-school variac at Siedse’s workstation immediately stands out. This heavy apparatus is an “auto transformer” without mains isolation and it is used in particular to test mains adapters for correct output voltage and current. “Such mains adapters are supplied with our equipment and then you do want to know whether they meet the specifications at all those different mains voltages in the world such as 110 V, 115 V, 240 V, and so on” explains Siedse. “Anyone can print a specification on the plastic box, but measuring is knowing for sure. With such an adapter, I look at stability, heat development, ripple, and resistance to voltage spikes — all under real and peak load conditions. An old variac is just ideal for that”. Even when a suitable type of mains adapter has been found and purchased in volume, Siedse will put samples through their paces.
|
In Sound and Pictures
Elektor paid a video visit to InnoFaith in Eindhoven. You can watch the video here: