Open Hardware Combats the Virus
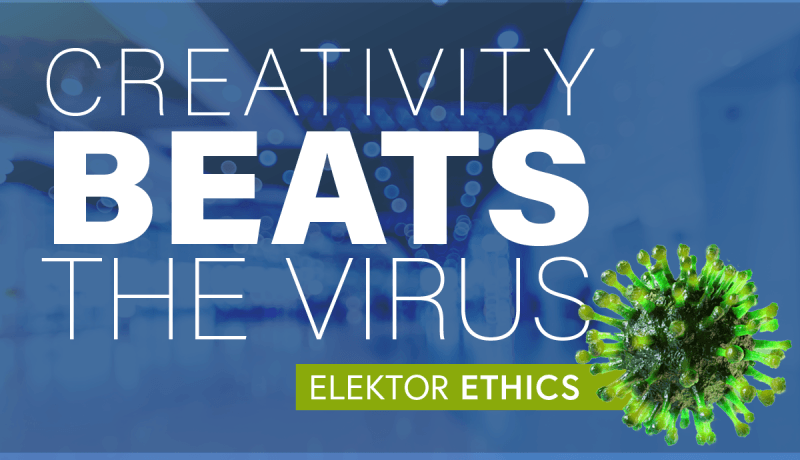
“The aim is to scale up at the global level by using open hardware designs.” This message comes from Professor Neil Gershenfeld, Director of the Center for Bits and Atoms at the Massachusetts Institute of Technology (MIT). Combating the corona virus is being hampered by a shortage of medical equipment, such as face masks and ventilators. The demand has increased enormously, while at the same time the supply is under pressure. The pandemic has disrupted global supply chains, seriously hindering the production and distribution of medical equipment. In an online video conference, Neil Gershenfeld described how open hardware can help to eliminate the shortages.
Open hardware
Just like open source software, open hardware can be used freely by everyone. Open hardware designs may be built, copied, shared and modified. If an open design for a protective face mask is developed in Belgium, for example, it can be made and distributed locally everywhere in the world. People from around the world with various backgrounds participated in the online conference – specialists in medical equipment, employees of Airbus and Philips, an Italian doctor, and people from the maker community.Help, don’t hurt
The first principle is ‘help, don’t hurt’. A face mask that doesn’t work properly is more harmful than no face mask at all, because it gives a false sense of safety. This is why the open hardware must be developed in consultation with medical specialists and approved by experts. A representative of the FDA, the US agency responsible for supervising medical equipment, said during the conference that the approval procedures would be accelerated. Approval would normally take several months, but now they are trying to do it in a few days.Prototyping and testing
The second principle is combining test capacity. Designs for face masks, for example, have to be tested to see if they actually block particles the size of a virus. Prototypes can be tested at locations where specialised equipment is available, such as the labs of MIT and the R&D departments of companies. The progress of the various projects is tracked in a GitLab repository. If a prototype fulfils all the medical requirements, the design can be made available online and can in principle be produced everywhere in the world. However, it must be borne mind that approval by a medical supervision authority in a given country is not automatically valid in other countries.Local production and distribution
Specialised equipment is necessary for prototype testing, but in many cases simpler machines are adequate for production. Neil Gershenfeld set up the first fabrication lab (Fab Lab) in 2001. A Fab Lab is a maker space with computer controlled machines such as laser cutters, CNC machines and 3D printers. Now there are more than 1750 Fab Labs spread over five continents. Each Fab Lab has the same resources, from the machine pool to the electronic components in the stock cabinet. The labs are also closely networked through via online platforms such as GitLab, and they operate on the open source principle. This means that a design conceived in the UCAL Fab Lab in Peru, for example, can be produced in the Oulu Fab Lab in Finland and further developed in the Kamakura Fab Lab in Japan.
The video conference participants discussed how this network effect can be applied to the production of medical equipment on a global scale. Expertise from various disciplines can be combined to create good designs. Prototypes can be tested in well-equipped labs, such as the MIT labs. Designs that meet the requirements can be shared via the Internet. As a result, Fab Labs and other maker spaces all over the world can start working on local production and distribution.
Face masks from 3D printers
There are already examples of how open hardware can be used to reduce the shortage of medical equipment. Josef Průša, the maker of the open source Prusa 3D printers, has created an open hardware design for protective face masks. 3D printers around the word are being used to produce face masks. The ULB Fab Lab in Brussels is also making face masks. In cooperation with the local hospital CHU Saint-Pierre, two prototypes have been developed: one for production with the laser cutter, and another for the 3D printer. After the prototypes were approved by the hospital, production was started up. Now Fab Labs in Charleroi and in the Ardennes have joined in to scale up production.
As Neil Gershenfeld said during the conference, “The vision is to use open hardware design, prototyping tools and a global production network so that we can scale up as fast as the virus.”