The LumenPnP Pick-and-Place Machine: An Interview with Its Creator Stephen Hawes
on
The Opulo LumenPnP (Figure 1), formally known as Index PnP by Index Machines, is a DIY pick-and-place machine (PnP). But what is a pick-and-place machine, and what can you do with one? Basically, it places components (usually SMD ones) on a PCB to be soldered later. The machines are practical if you need to populate more than just a dozen boards. For instance, such a machine is handy solution if you have a small series of different boards to produce, where an assembly service with its setup fees would be too expensive.
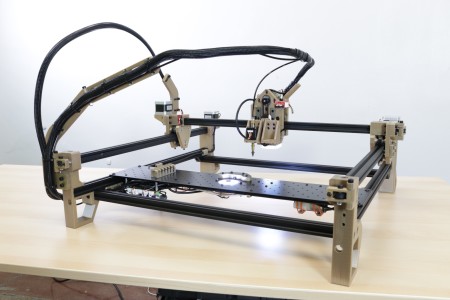
As helpful as these pick-and-place machines can be, they usually start at around $5000, they consume a lot of space, and getting spare parts or just a repair manual can be tricky. Things are different with the Opulo LumenPnP machine, and a kit for the machine (Figure 2) costs around $1200.
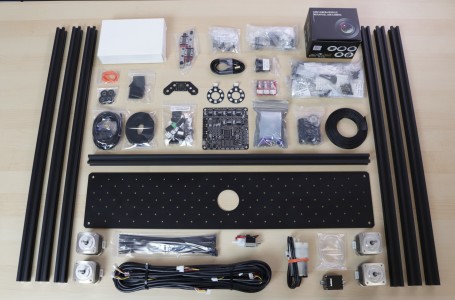
I conducted this interview in April 2022 and had a chance to talk to Stephen Hawes, creator of the LumenPnP, CEO and founder of Opulo.
Mathias Claußen: The last time we spoke was back in late 2020. Since then, you evolved your project into your own company. Tell us about yourself. What is your background?
Stephen Hawes: I was at Formlabs, the resin 3D printing company. That was a great job because I was on the sustaining engineering team, meaning I had to figure out how to fix problems that cropped up with machines in the field and how to do that with a piece of hardware that is already at someone’s place of business. Before Formlabs, I worked at a place called Deeplocal, which is technically an ad agency. But instead of making billboards or TV ads, we built prototypes and things. And in sometimes just over a week, I had to build a robot or some kind of thing. And then I flew all over the world to India, and China and Japan and the Netherlands and just all over the place, bringing them to conferences and shows. So it was really a good spectrum that I got from those two jobs to kind of see both ends of the scale of production.
Claußen: So, after your time at Formlabs you were going full time with your project, at that point called Index PnP?
Hawes: Yes, Index Machines was the name of the company. I started the company on April 14, 2021. And the goal was, after having quit my job, to be able to live from YouTube money, from making YouTube videos, and start the company around selling pick and place machines. I was working for myself and had my friend along with me. We were trying to make it happen and to get kits out the door.
Claußen: What was your motivation to create the machine in the first place?
Hawes: It started with a Kickstarter campaign in 2019, for a little light up bow tie that I called the Glowtie (Figure 3). I only had to make like 100. I was hand placing over 3000 components. I investigated getting them fabricated at an assembly house, like a lot of the PCB manufacturers will assemble them for you. And it over doubled my bill of materials cost. Then I investigated buying a pick and place machine to be able to use it. The only thing that could reasonably help me was like $10,000, I couldn’t afford that either. This weird in-between, where you’re making like 500 to 5000 units a year, where there’s not a ton of really good ways to make things at that moderate quantity. Assembling those things, it felt like there was a niche to fill. So, I decided to start working on it, the pick and place machine.

Claußen: I see that you moved to a new house and did the typical startup thing: you moved your company and all its stuff into your garage.
Hawes: Exactly. The rent I was paying right outside of Boston was unbelievably high. I had been saving up when I was working for Formlabs to buy a house and real estate in Pittsburgh, Pennsylvania (where I live now) is inexpensive and my mortgage is inexpensive. So, I can get away with it. It was an inexpensive space that I could be able to pay for with money from YouTube and my Patreon. That was exactly what we needed to get our feet underneath us and be able to get going and working out of a garage. There were times when we had vendors coming through for a meeting and we would just sit on a bunch of folding chairs in my garage and trying desperately to be as professional as we could. But sitting on folding chairs in the garage is not so professional. So, you know, but we had to make it work and we figured out how to do it. There were a couple of funny instances like that.
Claußen: Having patrons supporting you, and the fact that all stuff is on GitHub, how did the community help to improve the pick-and-place machine?
Hawes: The community gave us a tremendous amount of feedback. The easiest way to receive feedback from the community is through YouTube comments, and I read all of them, but I don’t have time to respond to all. Many people have incredibly good advice about how to solve problems that I’m struggling with. Sometimes in the video, I’ll just come out right and say, “I don't know how to solve this, if you think you have a solution, please let me know”. All these other people, many with advanced degrees in electrical engineering and mechanical engineering, have a really good idea about how to solve the problem. And they graciously share their time with me by providing that insight. So not only through YouTube comments, but also through GitHub pull requests where they make changes to the GitHub repo and request to merge it back into the project. Or just making an issue on GitHub is a great way to do it too. Just letting us know that there’s a problem about some specific way that they’re using the machine that isn’t quite right. And then we have a big Discord server with like 2700 people in it. It’s an active community full of builders, and now people who bought the kits are giving us a ton of feedback about the design and making modifications and improvements and all kinds of things.
Claußen: While sitting in the garage, you somehow were able to get some investment capital. Were looking for that? How did that happen? Were you just at the right place at the right time?
Hawes: Kind of. I always knew that I wanted to build a company around the pick-and-place machine. But I always figured that it would be bootstrapped. And it would go as fast as it could but as slow as it needed to be, to be able to just build it based on sales. We had an excellent opportunity from Joel Spolsky, who’s the co-founder of Fog Creek software, Stack Overflow and Trello. And he reached out. He was a patron of mine, and he had been for about a year. And after I made a video saying, “Hey, I'm going to start a company out of this and sell kits,” he reached out on Patreon about becoming an angel investor. And we had received quite a few inquiries from venture capitalist firms. But a lot of them didn’t fit our goals for the project and what we want to do with the company. Joel understood what we were doing and wanted it to continue going in that direction. He’s a wonderful human being. That was why we decided to go for it. I’ve always been kind of a little hesitant to take venture capital money because it felt like a loss of control. I did not want to sacrifice keeping the project open. That was incredibly important to me. But taking venture capital doesn’t necessarily mean that you must give up on your ethos for the company. It’s possible to do both. It took a lot of time and convincing and looking into it for me to effectively decide to go for it. But it’s been fantastic. Joel is a wonderful mentor and advisor. And we grew so much faster than we could have otherwise. We were not looking for it. I was planning on bootstrapping until he reached out.
Claußen: As your machine uses Marlin, firmware for the 3D printer, you were able to add a configuration file for the LumenPnP to the project's GitHub repository. This makes the LumenPnP an officially Marlin-supported “3D printer.” Was it hard to convince them to add a 3D printer that’s not 3D printing?
Hawes: That’s an excellent question. No, it was not hard. Scott, who’s the lead developer of Marlin, is a wonderful person and very helpful and kind. He was fantastic for helping us get our configuration merged into Marlin. But there are some features that were not supported by Marlin, namely being able to talk over an RS485 port, being able to communicate out of another serial port through an RS485 bus. At that time, Marlin didn’t support it. But we have a prototype and we're working on getting that merged upstream right now too. So, you can do a lot of stuff with Marlin that is not explicitly 3D printing. It really works stellar for a pick and place application.
Claußen: With RS485 mentioned, we come to the next question about the machine, the tape feeder. They are currently still in beta and officially production ready but coming to the machine. How did you start with a design for your tape feeder? You need to peel the tape from the reels and just feed one component to the machine.
Hawes: It is a resoundingly tricky problem, which seems like it would be very simple. If you’re just moving tape forward, it’s not that hard. But when you have to do it down to plus or minus, 100 micron - 200 micron (0.1 mm – 0.2 mm) accuracy, it starts to become a really challenging thing along with peeling the film. Also, being able to remove them easily. Hold the whole spool, communicate back to the machine, a ton of things go into it. When I started designing it a few years ago, I had this huge monster document of auditing every single existing feeder design that I could find, seeing the way that they go about doing it, what motor choice they have, what’s their communication protocol, how do they make sure that they’re moving the right distances, encoders, and optical sensor, all of this. I effectively did an audit of the current state of the art of hobbyist feeders. And I use that as a ton of reference and constantly have that open when I’m working on the feeders. We’ve learned a lot by doing a handful of prototypes and trying a few different things. Right now, the feeders do work, and we can use them in production. But I’m looking into making the feeder work more reliably and more consistently. It is still a huge improvement at the state that they are right now, but it’s not quite to the point where we feel comfortable putting it out there in selling it. All the source is still available online, you can go and download it and build it yourself if you’d like. But we’re going through some tweaks before we’re getting it out the door. Looking at other designs is an incredibly good way to see ways that people have solved problems before. There are so many variables going on, that dictates how you go about building it. But it’s been fun working on it. And we’re hopefully going to have a good stable release coming out pretty soon.
Claußen: You’re still using an AVR on the feeder itself. If you would start now, would you consider an RP2040 for it?
Hawes: We are not currently using AVR. For some of the more recent versions of the feeder, we switched to an STM32. The RP2040 is something that we’ve been looking at, especially with how available it is. The silicon shortage that has been happening has been pretty challenging for us. Availability is a huge consideration. I’m working on looking at making modifications to the feeder PCB right now. And RP2040 is something that I’m considering. There’re a couple of very specific things that we need in the microcontroller. We need a 96-bit UID etched into the silicon for authenticity. We can track which feeder is which, which actual piece of hardware. That’s an important part of our protocol. You can swap feeders in different slots, and the machine can keep track of where it went, which is pretty stellar. So, there are a couple of requirements that we have there. But the RP2040 is definitely something that we’re considering for the feeder boards.
Claußen: Construction files for the machine are on GitHub. Everybody could rebuild the machine from the current files. With the business you’ve started, will you still take that open approach? Or will there be a time when you say you need to make money and stop this openness?
Hawes: No, we are completely committed to keeping this project open source. It would not exist, if not for dozens of other existing open-source projects and the amount of support. And I mean even not in an ethos approach, but a pragmatic approach. The amount of feedback from community has been incredible, which would not be possible if not for being open source. Even just pragmatically looking at the benefits of keeping it open, it’s an easy win. There’s also the ethos of the thing where I just think it’s important to keep hardware open. I think that’s an incredibly important thing to do, putting stuff out there. If someone decided that they wanted to fix a problem with the board, they can go and see the actual design and do it. Ultimately, my goal is to make it easier to make your own PCBAs. That is what I’m trying to accomplish. If people don’t have the money to buy one from us, they can build one themselves. I want them to do it, I want them to have the machine. That’s the most important to me. Obviously, I want Opulo to continue to work. We are the driving force behind the project and if we still exist, we’re still adding to that goal. But, what I want is to make it easier to manufacture your own PCBAs. And I truly believe that by keeping it open we will help achieve that goal.
Claußen: About selling your kits ... anybody could rebuild the machine or make cheap knockoffs. There are entities out there that are good at copying hardware and selling them with bad documentation.
Hawes: Knockoffs are a part of working in the hardware industry. And I truly believe that they would come even if we weren’t open source. I don’t think that being open is necessarily leading to that, and it’s going to happen no matter. But I see knockoffs as not the terrible thing that I think a lot of other people do. Knockoff says that there is a market for this product, and that people want this thing. And if people are making knockoffs of it, it means that other people are getting a machine that will help them. Now, I can’t speak about the quality and how well it works and how well it’s supported. I think what Opulo will do to stand apart is, we have incredibly good documentation, we have a customer support team, and we also are the ones who are making the most changes and updates and innovations to this desktop pick and place machine. Going with an Opulo machine means that you’re going to be able to be supported for a ton of future updates and new features and making a lot better ease of use. Knockoffs are inevitable. We’re aware that it’s a thing that can happen. But it’s also a part of being in this business. We’re going to roll with it and see what happens.
Claußen: As you are now trying to ramp up production, getting some parts, especially with an STM stamp on them is not as easy as two years ago. If you get any, I think they have become expensive?
Hawes: They have become very expensive. The main chip on our motherboard is an STM32F407. At the time of designing it, I think it was like $3.89 at quantity one. But now it’s like $32. It is insane, I think at quantity 100 is at $16 apiece. An astronomical increase of price. We had to reassess a couple things when that started to happen. But honestly, that was a secondary consideration. If we could even get them was mostly the problem. We now have all our inventory tracked in a PLM software, but I would literally have a whole Chrome window open with eight tabs, with all of the ICs that we were worried about procuring. Every 30 minutes, I would refresh all of the pages. And I would look at many different vendors, and all the different parts we need, if they were somewhere in stock. And if I had the money, I pulled the trigger on it. So, we could at least know that we could produce more for kits. It’s also hard to justify redesigning a board around a chip that’s available right now. Because in two months, that chip might be unavailable. And the one that you had before might be super prolific. You are also making an entire open-source community go through these changes with you as well. It’s not just you and your own supply chain getting affected. It’s affecting all the people who are contributing to the project. It’s very hard to justify changing it. So far, we’re keeping an eye on what chips are available and when, hoping that prices go down a little bit so we don’t have to deal with crazy 4x chip cost increases. Being able to produce our own boards in house and assemble our own PCBAs has been nice. For as soon as we get chips in from any assortment of vendors, we’re the ones that are putting the boards together, so we can do all of our own sourcing. Keeping it all in house has been really nice. We were able to deal with a silicone shortage.
Claußen: There is a silicon shortage. There is also the problem that customers can’t put stuff in the pick-and-place machine.
Hawes: It doesn’t affect just us. It affects our customers and our users, our community. Not having the ability to get those chips is hard. What I’ve seen is a lot of people have still continued to pursue either a hobby if they’re a Tindie seller, and it’s not their full-time thing. It hasn’t prevented people from making stuff. It just means people have gotten more creative and craftier about how to solve the problem. Being able to keep the manufacturing in house means you’re not hoping that your contract manufacturer is able to track down the parts for you. You can do it yourself. You can go and find those parts, test them in house, and make sure that it works. That sourcing helps a lot. Although it has been challenging for our customers, they find a way around it. They find different chips, they redesign things, things like the SparkFun micro mod, where you just drop in a little edge slot board with a different microcontroller. So, yeah, we’ve all been finding a way somehow.
Claußen: What are your plans for the future? The feeder for the machine is one thing that is coming. Is more on its way?
Hawes: Right now, we have kits that are available. It’s our official 2.0 release that has happened. This is now an official stable thing that you can buy or build and use to accomplish a goal. And it’s not going to be a struggle, you’re going to be able to get it set up and you're going to be able to have it do useful work for you. So that was our 2.0 release. And that was when we started selling kits.
We’ve been making a ton of little improvements and tweaks mostly to the 3D printed parts and to documentation. Since then, we’ve been getting a ton of feedback from users, which has been great. We are aggressively working on getting feeders available for sale. That is a huge thing that our customers want. People using this machine don’t want to have to deal with strip feeders. With a couple staging plates, you definitely have the ability to get a good number of parts there, for the nozzle to pick up. But powered feeders are really where the machine will shine. And we’ve seen that from our internal testing just how easy it is to just let it run completely hands off. It’s been absolutely stellar. So powered feeders are a huge thing for us. We also don’t want to have people print their own parts. The kit that we currently sell is what we call a BYOP, bring your own printer. The kit comes with everything you need to build your own LumenPnP, but no printed parts. You print yourself. We’re also looking to rectify that so that they don't have to do all the assembly from scratch. And there’s a more assembled option for folks that don’t want to make a day out of building it. These are people that are buying this thing to solve the problem. And we want to solve that problem as easily and as smoothly as we can. And we have a lot of plans for a lot of other things down the road, which we’re exploring with R&D. I’ll probably end up making a couple of videos about that on the YouTube channel coming up about what we’re planning on working on but we’re just getting started. We’ve got a lot of other stuff in the works.
Claußen: My last question: Will we be able to get it somewhere in Europe? I mean, shipping from the US is not that cheap in general. Will Elektor be able to sell or resell the machine at a certain point?
Hawes: Very well could be. Right now, we really liked keeping all of our stock in house, because that means that if we’d make a change to the design, we can roll it out on the line tomorrow. If we ship a whole bunch of parts out to a distributor in Europe, they might not be the absolute most up to date. We are still exploring the idea of it because ultimately, it’s not going to be that big of a delay. Some slightly out of date kits, which have a tiny little improvement, are still going to be sitting in a warehouse. And those machines will still solve the customer's problem, whoever bought them. But we really liked the idea of being able to roll a change out on the line immediately. And all future kits sold from that day forward have that improvement. We’re weighing the pros and cons of it; we’re also dealing with a lot of the shipping costs going to Europe. It’s not as cheap as it could be. We are still exploring the idea of having a distributor in Europe.
Author's Note: Thanks to Stephen Hawes for giving some insights into the LumenPnP Machine and the process of starting his own business. If you are interested in the pick-and-place machine, you can find all information on GitHub. Moreover, if you would like to see the development of the LumenPnP over the years, check out Stephen Hawes YouTube channel. And if you feel you like to have one of these PnP machines, you may check them out at the Opulo homepage. Next thing to do for me is to convince our management that the Elektor Labs needs one. Maybe we can get one as a Christmas present?
Discussion (2 comments)
NuttyProf 2 years ago
Mathias_Claussen(Elektor) 2 years ago
thanks for your feedback. If you want to contribute to the project may hit over to their discord server ( https://discordapp.com/invite/TCwy6De ) or fill a bug report ( in this case feature request ) on their github page ( https://github.com/opulo-inc/lumenpnp ) . This will avoid the man in the middle.
Best Regards
Mathias Claußen