3D printers going for $5000 a pop
April 21, 2011
on
on
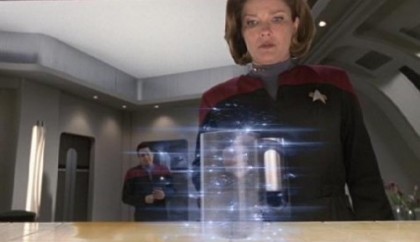
Ever since we saw it in Star Trek we all want one: a Replicator. A Replicator can create any inanimate object from waste matter. With the arrival of 3D printers, technological development has once again caught up with sci-fi’s far out imagination.
3D printing works exactly as it sounds. Feed a 3D model data file to a computer and hit the print command. The printer then makes use of additive techniques by applying layer upon layer of material such as plastic or steel, replicating the digital 3D model in actual matter. This is done by slicing the 3D model into layers and creating a 2D image for each slice. These 2D images are then printed unto powdered materials, adding layer upon layer.
But at prices of over a $ 100,000 it’s hard to claim the Replicator has been democratized. But in the New York Times video embedded below CEO Carl Bass of Autodesk, a company that designs software to drive 3D printers, says there will soon be printers on the market for an affordable $5000,-.
3D printing can contribute to a sustainable economy by reducing transport. Instead of shipping goods around the world in the future we’ll just download a 3D model and print the stuff at home. The November ’10 broadcast of BBC’s Digital Planet hosts an interview with Adrian Bowyer and David Flanders who built a self-replicating machine. A 3D printer that prints 3D printers. It’s called Reprap, short for Rapid Replicator. The price of a Reprap is only $500,-. But it gets better, they’re given away for free. As long as you promise to give away the first Reprap you printed as well.
Flanders sees many opportunities for emerging economies. Low-cost shoes for children can be printed. When the child has grown out of them, the digital model for the shoe can be enlarged by 0.03 percent. And because the replicator’s printing material is reusable, the old shoe can be fed back to the printer. A plastic milk bottle can be added for increased volume and a new pair of shoes materializes from the replicator.
3D printing works exactly as it sounds. Feed a 3D model data file to a computer and hit the print command. The printer then makes use of additive techniques by applying layer upon layer of material such as plastic or steel, replicating the digital 3D model in actual matter. This is done by slicing the 3D model into layers and creating a 2D image for each slice. These 2D images are then printed unto powdered materials, adding layer upon layer.
But at prices of over a $ 100,000 it’s hard to claim the Replicator has been democratized. But in the New York Times video embedded below CEO Carl Bass of Autodesk, a company that designs software to drive 3D printers, says there will soon be printers on the market for an affordable $5000,-.
3D printing can contribute to a sustainable economy by reducing transport. Instead of shipping goods around the world in the future we’ll just download a 3D model and print the stuff at home. The November ’10 broadcast of BBC’s Digital Planet hosts an interview with Adrian Bowyer and David Flanders who built a self-replicating machine. A 3D printer that prints 3D printers. It’s called Reprap, short for Rapid Replicator. The price of a Reprap is only $500,-. But it gets better, they’re given away for free. As long as you promise to give away the first Reprap you printed as well.
Flanders sees many opportunities for emerging economies. Low-cost shoes for children can be printed. When the child has grown out of them, the digital model for the shoe can be enlarged by 0.03 percent. And because the replicator’s printing material is reusable, the old shoe can be fed back to the printer. A plastic milk bottle can be added for increased volume and a new pair of shoes materializes from the replicator.
Read full article
Hide full article
Discussion (0 comments)