3D Printing Beats Mass Production In Energy Efficiency
October 11, 2013
on
on
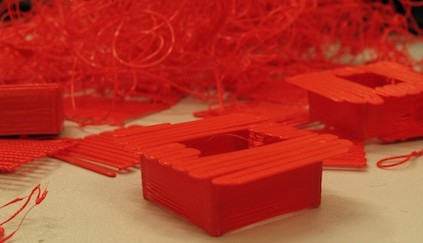
A study from Michigan Technology University shows 3D printed products require 41% to 74% less energy than large-scale manufactured goods.
Since the First Industrial Revolution manufacturing has gone through stages of increasing centralization. But with the emergence of affordable open source 3D printers the pendulum may swing back to decentralized home-based production.
Megan Kreiger and Joshua M. Pearce of Michigan Technology University did a comparative study [PDF] of energy demand and greenhouse gas emissions of centralized and distributed manufactured goods. The scope of the study is small plastic products because they are perfectly suited for 3D printed home production.
Currently, plastics are mostly mass-manufactured in low-cost labor countries and shipped across the globe. In terms of energy consumption, home-based 3D printing has the obvious advantage of avoiding international transportation costs. Another important factor is the improved material efficiency of additive manufacturing.
The conventional method to create plastic components is to inject heated thermoplastics into a mold. Injection molding leaves little room for material manipulation, the parts are always solid plastic. Kreiger and Pearce found that for most 3D prints a fill percentage of 25% or less was enough to maintain the structural integrity of the product. Moreover, 3D printing allows for creating complex forms in a single session such as moving parts and hollow structures, saving energy on drilling and assembly machinery.
To compare distributed and conventional manufacturing Kreiger and Pearce, did a Life Cycle Analysis of three products: a citrus juicer, a children's building block and a water spout. For each product they calculated the total Cumulative Energy Demand from cradle-to-gate. The conventional LCA includes raw material extraction in the country of production, mass-production and international transportation to a warehouse in the US. The distributed LCA includes raw material extraction in the US, domestic transportation and home-based production.
The researchers also experimented with solar powered 3D printers. Here they achieved the best result, saving 74% energy compared to conventional manufacturing. For non-renewable sourced electricity the best result was 64%.
Kreiger and Pearce expect that as consumer grade 3D print technology matures, energy efficiency will further improve.
Photo: Thijs Beckers
Via: gigaom.com
Since the First Industrial Revolution manufacturing has gone through stages of increasing centralization. But with the emergence of affordable open source 3D printers the pendulum may swing back to decentralized home-based production.
Megan Kreiger and Joshua M. Pearce of Michigan Technology University did a comparative study [PDF] of energy demand and greenhouse gas emissions of centralized and distributed manufactured goods. The scope of the study is small plastic products because they are perfectly suited for 3D printed home production.
Currently, plastics are mostly mass-manufactured in low-cost labor countries and shipped across the globe. In terms of energy consumption, home-based 3D printing has the obvious advantage of avoiding international transportation costs. Another important factor is the improved material efficiency of additive manufacturing.
The conventional method to create plastic components is to inject heated thermoplastics into a mold. Injection molding leaves little room for material manipulation, the parts are always solid plastic. Kreiger and Pearce found that for most 3D prints a fill percentage of 25% or less was enough to maintain the structural integrity of the product. Moreover, 3D printing allows for creating complex forms in a single session such as moving parts and hollow structures, saving energy on drilling and assembly machinery.
To compare distributed and conventional manufacturing Kreiger and Pearce, did a Life Cycle Analysis of three products: a citrus juicer, a children's building block and a water spout. For each product they calculated the total Cumulative Energy Demand from cradle-to-gate. The conventional LCA includes raw material extraction in the country of production, mass-production and international transportation to a warehouse in the US. The distributed LCA includes raw material extraction in the US, domestic transportation and home-based production.
The researchers also experimented with solar powered 3D printers. Here they achieved the best result, saving 74% energy compared to conventional manufacturing. For non-renewable sourced electricity the best result was 64%.
Kreiger and Pearce expect that as consumer grade 3D print technology matures, energy efficiency will further improve.
Photo: Thijs Beckers
Via: gigaom.com
Read full article
Hide full article
Discussion (0 comments)