Before Hall-effect devices....
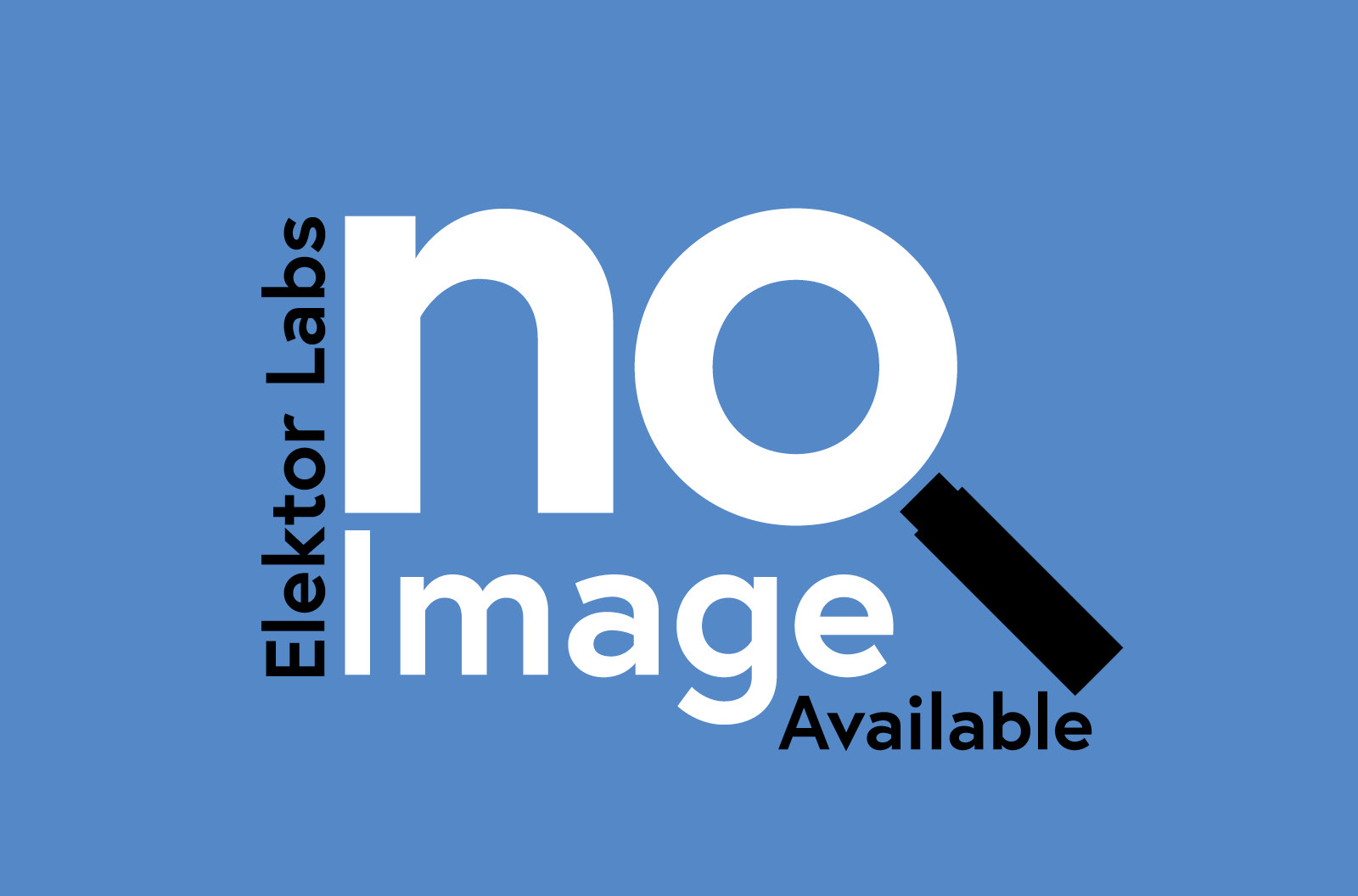
I want to create a measurement circuit for measuring specifically D.C. current using 'old-school' inductive techniques.
Before Hall effect devices became ubiquitous in clampmeters for current measurement there were some current clamps marketed that could measure D.C. currents using inductive principles - obviously a bit more cunning than the more straightforward task of A.C. current measurement. I am intending to undertake a project to accurately measure D.C. current using inductive techniques and I wish to authoritatively employks these (now) little-known methods. Does anyone have any technical information they can provide me? Patent references would also be useful. Thanks.
Discussion (1 comment)
erayzor 3 years ago
I guess you are interested in measuring DC currents without galvanic contact, especially without the necessity to cut the wire carrying the current; correct?
In principle, you only have to measure the strength of the magnetic field around the wire, but this field is very inhomogeneous (dropping with the distance r proportional to 1/r). Therefore, for reliable results you either have to control (or measure) the distance accurately, or you are using a toroid made of "soft" magnetic material (like soft iron or ferrite) and high magnetic permeability µ around the wire to concentrate virtually the complete magnetic flux inside the toroid.
This technique is used in the current "clamp" you mention also. Typically, the toroid is cut in two halves, allowing to close it around the wire and to place a magnetic field detector in one of the gaps. The remaining gaps should be as small as possible - typically well below 1 mm - to keep the magnetic flux inside the toroid.
When the accuracy of the current measurement shall be high, typically a compensation coil is wound around the toroid, having a known turn ratio relative to the "primary" wire (or coil) carrying the current to be measured. The signal of the magnetic field sensor is used to send a current through the "secondary" coil which creates a magnetic flux of opposite sign relative to that of the primary wire (or coil). A feedback loop using an operational amplifier continously tries to cancel out ("zero") the net magnetic field measured by the sensor.
Thus, the current through the secondary coil is strictly proportional to the current through the primary wire (or coil). Using an appropriate turn ratio (typically in the range of 100 to 10.000), the secondary current is in a range of e.g. +/- 20 mA (or less), which can be easily controlled and measured accurately (e.g. using a precision resistor and a voltmeter). The whole device can be viewed as a transformer for DC currents ("DC" can include frequencies of up to several 100 kHz).
As mentioned by you, virtually all modern devices are using Hall effect sensors. I am not aware of actual devices (or patents) using alternative sensors, but those alternatives exist and most probably some of them have been used (and patented) for DC current measurements before high-quality Hall effect sensors became readily available.
One option is to exploit the effect of magnetic saturation, one major aspect of the non-linear behaviour of magnetic materials. Qualitatively spoken, the ability of such materials to enhance a magnetic field is limited; the limit is characterized by the saturation flux density. At low flux densities, the permeability µ is high (e.g. 100 or even 100.000, depending on the material), resulting in a strongly enhanced field; in this case, the inductivity L of a coil with a core made of magnetic material is much higher than without. At flux densities close to (or higher than) the saturation flux density, the enhancement drops (µ approaches 1 asymptotically); in this case, the inductivity L of the coil with a core of magnetic material is not much higher than without.
Therefore, one of the gaps of the toroid - which can be several millimeters wide in this case - can be (partially) filled with an appropriate soft magnetic material, either having a significantly lower saturation flux density than the material of the toroid, or having a much smaller cross section, leading to a higher flux density inside the gap filling material compared to that inside the toroid material. In both cases, a small ("tertiary") coil closely wound around the gap filling material can be used to detect the strength of the magnetic flux inside the toroid. For example, in combination with an adequate capacitor C, the small coil with inductivity L can be used as a part of an oscillator having a frequency f proportional to 1/sqrt(LC). When measuring the frequency of this oscillator, the change of inductivity L of the small coil can be detected.
To identify the optimal operation point (regarding the nominal magnetic flux inside the toroid) of the device, the frequency f of the oscillator has to be recorded versus the current I flowing through the secondary (or primary) coil. The optimal current I_OP is found where the change in frequency f(I) when changing the current I (df/dI) is maximum. The feedback loop mentioned above now has to keep the frequency f of the oscillator constant while the current through the primary wire (or coil) is changing. As in the case of a Hall sensor device, the current through the secondary coil is proportional to the primary current. The only difference is the offset due to the current I_OP required for reaching the operating point; this disadvantage can be avoided by using a separate coil for I_OP.
xylstra 3 years ago
Thanks again.