Potential-free current measurement for oscilloscopes [150170]
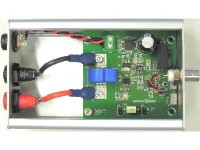
Using a current transducer with galvanic isolation between input and output this circuit can be used for safe measurements of currents up to 25 A rms
Modification of a circuit designed by
Karsten Böhme
(Messwandler zur potentialfreien Strommessung für Oszilloskope)
Electrical current can be measured in different ways. Usually this is done with a measuring resistor, over which the falling voltage is measured. For most oscilloscopes, however, the grounding of the signal input is connected to the protective earth of the mains voltage. A current measurement with a measuring resistor is thus not possible in many cases. Current clamps can measure the current without potential, but are not suitable for fast measurements, especially since they usually have no connection for an oscilloscope. Anyone who wants to measure electric currents with their oscilloscope galvanically isolated, can’t avoid the use of a current clamp for oscilloscopes. The problem for most electronics enthusiasts is, however, the high price for a current clamp, which can exceed the price of a simple digital storage oscilloscope. In view of such high prices, it is already surprising that there are apparently no DIY projects in this direction. Especially in the field of power electronics, the measurement of high-frequency currents at the oscilloscope is often indispensable.
The circuit presented here shows that a potential-free current measurement can be realized with relatively few but high-quality components. Current transducers on the basis of Hall effect sensors are basically nothing new, but only through an additional circuit are the measured currents optimally adapted to the oscilloscope. The focal point of the circuit is the LTS 25-NP current transducer from LEM. This current transducer measures the current indirectly via a Hall sensor and thus enables a potential-free current measurement. By connecting the LTS 25-NP terminals in different ways, three measuring ranges ± 8 A, ± 12 A and ± 25 A are possible. This circuit was designed as a ± 25 A version by connecting the three current measuring pins on each side. The bandwidth of the current transducer ranges from DC to 200 kHz at -0.5 dB ... 1 dB. The accuracy is given by the manufacturer with ± 0.7 %. The output voltage of the current transducer is exactly 2.5 V at 0 A. A current of 1 A results in a 25 mV increase or decrease in the output voltage. For the representation of small constant currents on the oscilloscope, an output voltage of 2.5 V at 0 A is rather unsuitable. Better would be a representation in which the output voltage starts from 0 V. This circuit ensures this shift so that a current of 0 A to 25 A produces an output voltage of 0V to 2.5V. Thus, the currents to be measured can be represented in the optimum measuring ranges of the oscilloscope.
The following signals are provided on the PCB.
K4: output intended for a BNC connector. Measurement of currents up to 25A. The gain of the output signal is adjustable via a switch (S2, total gain 4 x or 10 x). This output also contains a low-pass filter (R7/C4) with a cut-off frequency of 24Hz that can be switch on or off (S1).
K5: output signal from LTS 25-NP. Measurement of AC and DC currents of ± 25A (2.5 V offset).
K6: output signal from LTS 25-NP. Measurement of AC currents ± 25A.
The amplifier stages
The output of the LEM 25-NP (MOD1) is buffered by a Zero-Drift Rail-to-Rail Input/Output amplifier (IC1A) ensuring the output signal of MOD1 is not degraded in any way by the input impedance of the first amplifier stage (IC2B). The first amplifier is also used to get rid of the 2.5 V offset of MOD1. Trimmer P1 is added to adjust K4 to exactly 0 V (leave current measurement connectors K2 and K3 open). The range of P1 is limited by R1 and R2 to provide a smoother adjustment. The second amplifier from IC1 is used to buffer the voltage of P1. This way the gain of IC2B is independent of the changing output impedance when P1 is adjusted. To increase bandwidth at the second amplifier stage its gain has to be less. Total gain is now divided over two stages. IC2B amplifies by factor of two. The next amplifier IC2A amplifies two or five times and sets total gain to 4 and 10 times respectively. The higher gain option is added to have a higher sensitivity (250 mV/A instead of 100 mV/A). IC2 is a Precision, Rail-to-Rail Input/Output, Low Offset Voltage amplifier. It has a very low offset voltage (±250 µV max.), offset voltage drift (±2.5 µV max.) and low bias current (±5 pA max.). At a GBW of 10 MHz and a gain setting of 5 the bandwidth of IC2A is still 2 MHz. This is more than 10 times the bandwidth of MOD1. Total bandwidth of IC2A and IC2B will of course be a little less.
Power supply
The circuit should be able to process AC currents and so the signal on K4 should be able to go equally negative as positive. IC1 handles signals with an offset of 2.5 V and only needs a single +5 V power supply. However the outputs of IC2 have signals with no additional offset and so IC2 needs a negative power supply. If the circuit is powered by a single DC voltage (K1) a negative power supply can only be generated by a DC/DC converter. To keep the extra components needed then to a minimum an isolated single output 1 W DC/DC converter module with regulated output is used (MOD2). To suppress switching artifacts two inductors are added. The positive output (+Vout) is connected to ground and the negative output (-Vout) becomes the -5 V power supply. Since the -5 V is only used for IC2A it doesn’t need to have top specifications. The OPA2197 was used for IC2 because it can handle the 10 V total supply voltage, 36 V in fact.
The main +5 V supply also acts as a reference for divider R1/P1/R2. So it has to be accurate and have a very low temperature dependency. Instead of using a standard voltage regulator as a reference we turn it around. Let’s use a reference as a power supply. The LT1021 (IC3) is a precision reference with ultralow drift and noise, extremely good long term stability and almost total immunity to input voltage variations. One of the typical applications is ‘Boosted Output Current with Current Limit’. If the current drawn by the LT1021 (5 V version) is more than 2 mA the PNP transistor T1 supplies most of the extra needed current (UBE/R13). At a voltage of 1.7 V across LED1 the current drawn by the LT1021 is about 5 mA. The red led (LED1) parallel to R13 limits the maximum current T1 can source, roughly 90…100 mA ((ULED1 – UBE)/R12). LED1 will light up if the current reaches its maximum (indicates current limiting active).
The input voltage for the power supply can be a DC or AC power source. The minimum input voltage is set by the drop across B1 and the minimum voltage needed by the LT1021. The maximum input voltage is limited by MOD2 (18 V max.). When using a AC source don’t forget the peak voltage is maybe more than 1.4 times the indicated voltage. The null load voltage of small transformers can be 30 % higher or more. So the voltage of a small 12 V transformer can be too high!
The PCB, built-in prototype
When looking for a nice enclosure for our prototype we decided to use a metal enclosure from Hammond, 1455K1201. It’s about 123x78x43 mm (without the plastic frames). The surface of the PCB is larger than strictly needed, but the size was increased so it can slide into the slots in the inner sides of the enclosure (use the second slots from the bottom for safety). The PCB has four mounting holes in case a different enclosure is used, but the ones next to K2 and K3 can also be used to fasten the PCB inside the enclosure. The PCB is 70.5 mm long and the inside of the enclosure is 120 mm long. Preventing the PCB from sliding we used two 10 mm male-female metal M3 standoffs to fasten the PCB to the bottom (but you can also glue it or …). Two metal M3 washers between each standoff and PCB are added to fill the total distance. The two switches are placed on the very edge of the PCB. We placed the BNC connector (insulated, panel mount) in the middle of the front of the enclosure, just above the switches. The high current connections are made with M3 mounted faston terminals (K2, K3). 30 A rated panel mounted banana jacks are used to make the current inputs assessable on the enclosure. Use at least 2.5 mm2 stranded wire to connect the faston terminals to the banana jacks. On our prototype we used a DC power connector so a standard AC adapter can be used to power the circuit.
Specifications
Imax 25 A nominal current rms,
80 A pulsed (exceeds maximum output voltage)
Power supply current (K1) 50 mA (19.5 VDC)
44 mA (9.2 VDC)
Power supply min. DC 9.2 V (MOD2 shuts down)
Power supply max. DC 19.5 V (18 V at input MOD2)
Power supply AC 9..12 V
Sensitivity 100 mV/A (gain = 4)
250 mV/A (gain = 10)
Imax @ gain = 10 < 20 A (5 V max. output voltage)
Bill of material PCB 150170-1 v1.1
Resistor
R1,R2 = 12 kΩ, 1 %, 125 mW, SMD 0805
R3,R5,R10 = 10 kΩ, 0.1 %, 100 mW, SMD 0805
R4,R6 = 20 kΩ, 0.1 %, 125 mW, SMD 0805
R7 = 6.8 kΩ, 1 %, 125 mW, SMD 0805
R8 = 7.5 kΩ, 0.1 %, 250 mW, SMD 0805
R9 = 30 kΩ, 0.1 %, 100 mW, SMD 0805
R11 = 0 Ω, 100 mW, SMD 0805
R12 = 12 Ω. 1 %, 250 mW, SMD 1206
R13 = 330 Ω, 1 %, 125 mW, SMD 0805
R14 = 1 kΩ, 1 %, 125 mW, SMD 0805
P1 = 100 Ω, 20 %, 250 mW, SMD, Bourns 3314G-2-101E
Capacitor
C1,C2,C4 = 1 µF, 10 %, 50 V, SMD 0805, X7R
C3,C5 = 470 nF, 10 %, 50 V, SMD 0805
C6 = 1 µF, 5 %, 63 V, PET, lead spacing 5/7.5 mm
C7,C11 = 4.7 µF, 10 %, 50 V, SMD 1206, X7R
C8 = 4.7 µF, 10 %, 50 V, SMD 1210, X7R
C9,C10 = 100 nF, 10 %, 50 V, SMD 0805, X7R
C12 = 470 µF, 20 %, 50 V, lead spacing 5 mm, 13x21 mm
C13,C14,C15,C16 = 10 nF, 10 %, 100 V, SMD 0805, X7R
Inductor
L1 = 4.7 µH, 20 %, 1.2 A, 0.12 Ω, Bourns SRN3015TA-4R7M
L2 = 1 kΩ@100 MHz, 200 mA, 0.6 Ω, Laird HZ0603B102R-10
Semiconductor
B1 = DF04S, 400 V, 1.5 A, SMD SDIP 4L
LED1 = LED, red, 50 mcd, 1.85 V @ 20 mA, SMD 0805
LED2 = LED, green, 50 mcd, 2.1 V @ 20 mA, SMD 0805
T1 = FZT751, PNP, 60 V, 2 W, 3 A, SMD SOT-223
IC1 = AD8552ARZ, SMD SOIC-8
IC2 = OPA2197IDR, SMD SOIC-8
IC3 = LT1021DCS8-5#PBF, SOIC-8
MOD1 = LTS 25-NP, through hole module, LEM
MOD2 = TMR 1-1211, SIP module, Traco Power
Other
K1 = Terminal block, pitch 5.08 mm, 2-way
K2,K3 = 6.35 mm TAB, Faston, 3.3 mm, TE Connectivity 42822-2
K2,K3 = Faston terminal, 6.35 mm, female, blue, 14-16 AWG, 2.5 mm2
K4,K5,K6 = Pin header, 1x2, vertical, pitch 2.54 mm
K4,K5,K6 = Pin socket, 1x2, vertical, pitch 2.54 mm
S1,S2 = Slide switch, right angle, SPDT, On-On, 100 mA, OS102011MA1QN1 C & K Components
BNC Insulated Bulkhead Socket, Panel Mount, 5-1634504-1 Greenpar/TE Connectivity
DC Power connector, receptacle, 2.1 mm, 1 A, panel mount, isolated
Banana Test Connector, 4mm, Jack, Panel Mount, 30 A, Red, Cliff Electronic Components FCR14461
Banana Test Connector, 4mm, Jack, Panel Mount, 30 A, Black, Cliff Electronic Components, FCR14460
Metal Enclosure, Hammond 1455K1201, 78x123x43 mm
45 mm 2.5 mm2 stranded wire, red
45 mm 2.5 mm2 stranded wire, black
4 x washer, Plain, Steel, Zinc Plated, M3
2 x standoff, Zinc Plated, Steel, M3, Hex Male-Female, 10 mm
Misc.
PCB 150170-1 v1.1
Karsten Böhme
(Messwandler zur potentialfreien Strommessung für Oszilloskope)
Electrical current can be measured in different ways. Usually this is done with a measuring resistor, over which the falling voltage is measured. For most oscilloscopes, however, the grounding of the signal input is connected to the protective earth of the mains voltage. A current measurement with a measuring resistor is thus not possible in many cases. Current clamps can measure the current without potential, but are not suitable for fast measurements, especially since they usually have no connection for an oscilloscope. Anyone who wants to measure electric currents with their oscilloscope galvanically isolated, can’t avoid the use of a current clamp for oscilloscopes. The problem for most electronics enthusiasts is, however, the high price for a current clamp, which can exceed the price of a simple digital storage oscilloscope. In view of such high prices, it is already surprising that there are apparently no DIY projects in this direction. Especially in the field of power electronics, the measurement of high-frequency currents at the oscilloscope is often indispensable.
The circuit presented here shows that a potential-free current measurement can be realized with relatively few but high-quality components. Current transducers on the basis of Hall effect sensors are basically nothing new, but only through an additional circuit are the measured currents optimally adapted to the oscilloscope. The focal point of the circuit is the LTS 25-NP current transducer from LEM. This current transducer measures the current indirectly via a Hall sensor and thus enables a potential-free current measurement. By connecting the LTS 25-NP terminals in different ways, three measuring ranges ± 8 A, ± 12 A and ± 25 A are possible. This circuit was designed as a ± 25 A version by connecting the three current measuring pins on each side. The bandwidth of the current transducer ranges from DC to 200 kHz at -0.5 dB ... 1 dB. The accuracy is given by the manufacturer with ± 0.7 %. The output voltage of the current transducer is exactly 2.5 V at 0 A. A current of 1 A results in a 25 mV increase or decrease in the output voltage. For the representation of small constant currents on the oscilloscope, an output voltage of 2.5 V at 0 A is rather unsuitable. Better would be a representation in which the output voltage starts from 0 V. This circuit ensures this shift so that a current of 0 A to 25 A produces an output voltage of 0V to 2.5V. Thus, the currents to be measured can be represented in the optimum measuring ranges of the oscilloscope.
The following signals are provided on the PCB.
K4: output intended for a BNC connector. Measurement of currents up to 25A. The gain of the output signal is adjustable via a switch (S2, total gain 4 x or 10 x). This output also contains a low-pass filter (R7/C4) with a cut-off frequency of 24Hz that can be switch on or off (S1).
K5: output signal from LTS 25-NP. Measurement of AC and DC currents of ± 25A (2.5 V offset).
K6: output signal from LTS 25-NP. Measurement of AC currents ± 25A.
The amplifier stages
The output of the LEM 25-NP (MOD1) is buffered by a Zero-Drift Rail-to-Rail Input/Output amplifier (IC1A) ensuring the output signal of MOD1 is not degraded in any way by the input impedance of the first amplifier stage (IC2B). The first amplifier is also used to get rid of the 2.5 V offset of MOD1. Trimmer P1 is added to adjust K4 to exactly 0 V (leave current measurement connectors K2 and K3 open). The range of P1 is limited by R1 and R2 to provide a smoother adjustment. The second amplifier from IC1 is used to buffer the voltage of P1. This way the gain of IC2B is independent of the changing output impedance when P1 is adjusted. To increase bandwidth at the second amplifier stage its gain has to be less. Total gain is now divided over two stages. IC2B amplifies by factor of two. The next amplifier IC2A amplifies two or five times and sets total gain to 4 and 10 times respectively. The higher gain option is added to have a higher sensitivity (250 mV/A instead of 100 mV/A). IC2 is a Precision, Rail-to-Rail Input/Output, Low Offset Voltage amplifier. It has a very low offset voltage (±250 µV max.), offset voltage drift (±2.5 µV max.) and low bias current (±5 pA max.). At a GBW of 10 MHz and a gain setting of 5 the bandwidth of IC2A is still 2 MHz. This is more than 10 times the bandwidth of MOD1. Total bandwidth of IC2A and IC2B will of course be a little less.
Power supply
The circuit should be able to process AC currents and so the signal on K4 should be able to go equally negative as positive. IC1 handles signals with an offset of 2.5 V and only needs a single +5 V power supply. However the outputs of IC2 have signals with no additional offset and so IC2 needs a negative power supply. If the circuit is powered by a single DC voltage (K1) a negative power supply can only be generated by a DC/DC converter. To keep the extra components needed then to a minimum an isolated single output 1 W DC/DC converter module with regulated output is used (MOD2). To suppress switching artifacts two inductors are added. The positive output (+Vout) is connected to ground and the negative output (-Vout) becomes the -5 V power supply. Since the -5 V is only used for IC2A it doesn’t need to have top specifications. The OPA2197 was used for IC2 because it can handle the 10 V total supply voltage, 36 V in fact.
The main +5 V supply also acts as a reference for divider R1/P1/R2. So it has to be accurate and have a very low temperature dependency. Instead of using a standard voltage regulator as a reference we turn it around. Let’s use a reference as a power supply. The LT1021 (IC3) is a precision reference with ultralow drift and noise, extremely good long term stability and almost total immunity to input voltage variations. One of the typical applications is ‘Boosted Output Current with Current Limit’. If the current drawn by the LT1021 (5 V version) is more than 2 mA the PNP transistor T1 supplies most of the extra needed current (UBE/R13). At a voltage of 1.7 V across LED1 the current drawn by the LT1021 is about 5 mA. The red led (LED1) parallel to R13 limits the maximum current T1 can source, roughly 90…100 mA ((ULED1 – UBE)/R12). LED1 will light up if the current reaches its maximum (indicates current limiting active).
The input voltage for the power supply can be a DC or AC power source. The minimum input voltage is set by the drop across B1 and the minimum voltage needed by the LT1021. The maximum input voltage is limited by MOD2 (18 V max.). When using a AC source don’t forget the peak voltage is maybe more than 1.4 times the indicated voltage. The null load voltage of small transformers can be 30 % higher or more. So the voltage of a small 12 V transformer can be too high!
The PCB, built-in prototype
When looking for a nice enclosure for our prototype we decided to use a metal enclosure from Hammond, 1455K1201. It’s about 123x78x43 mm (without the plastic frames). The surface of the PCB is larger than strictly needed, but the size was increased so it can slide into the slots in the inner sides of the enclosure (use the second slots from the bottom for safety). The PCB has four mounting holes in case a different enclosure is used, but the ones next to K2 and K3 can also be used to fasten the PCB inside the enclosure. The PCB is 70.5 mm long and the inside of the enclosure is 120 mm long. Preventing the PCB from sliding we used two 10 mm male-female metal M3 standoffs to fasten the PCB to the bottom (but you can also glue it or …). Two metal M3 washers between each standoff and PCB are added to fill the total distance. The two switches are placed on the very edge of the PCB. We placed the BNC connector (insulated, panel mount) in the middle of the front of the enclosure, just above the switches. The high current connections are made with M3 mounted faston terminals (K2, K3). 30 A rated panel mounted banana jacks are used to make the current inputs assessable on the enclosure. Use at least 2.5 mm2 stranded wire to connect the faston terminals to the banana jacks. On our prototype we used a DC power connector so a standard AC adapter can be used to power the circuit.
Specifications
Imax 25 A nominal current rms,
80 A pulsed (exceeds maximum output voltage)
Power supply current (K1) 50 mA (19.5 VDC)
44 mA (9.2 VDC)
Power supply min. DC 9.2 V (MOD2 shuts down)
Power supply max. DC 19.5 V (18 V at input MOD2)
Power supply AC 9..12 V
Sensitivity 100 mV/A (gain = 4)
250 mV/A (gain = 10)
Imax @ gain = 10 < 20 A (5 V max. output voltage)
Bill of material PCB 150170-1 v1.1
Resistor
R1,R2 = 12 kΩ, 1 %, 125 mW, SMD 0805
R3,R5,R10 = 10 kΩ, 0.1 %, 100 mW, SMD 0805
R4,R6 = 20 kΩ, 0.1 %, 125 mW, SMD 0805
R7 = 6.8 kΩ, 1 %, 125 mW, SMD 0805
R8 = 7.5 kΩ, 0.1 %, 250 mW, SMD 0805
R9 = 30 kΩ, 0.1 %, 100 mW, SMD 0805
R11 = 0 Ω, 100 mW, SMD 0805
R12 = 12 Ω. 1 %, 250 mW, SMD 1206
R13 = 330 Ω, 1 %, 125 mW, SMD 0805
R14 = 1 kΩ, 1 %, 125 mW, SMD 0805
P1 = 100 Ω, 20 %, 250 mW, SMD, Bourns 3314G-2-101E
Capacitor
C1,C2,C4 = 1 µF, 10 %, 50 V, SMD 0805, X7R
C3,C5 = 470 nF, 10 %, 50 V, SMD 0805
C6 = 1 µF, 5 %, 63 V, PET, lead spacing 5/7.5 mm
C7,C11 = 4.7 µF, 10 %, 50 V, SMD 1206, X7R
C8 = 4.7 µF, 10 %, 50 V, SMD 1210, X7R
C9,C10 = 100 nF, 10 %, 50 V, SMD 0805, X7R
C12 = 470 µF, 20 %, 50 V, lead spacing 5 mm, 13x21 mm
C13,C14,C15,C16 = 10 nF, 10 %, 100 V, SMD 0805, X7R
Inductor
L1 = 4.7 µH, 20 %, 1.2 A, 0.12 Ω, Bourns SRN3015TA-4R7M
L2 = 1 kΩ@100 MHz, 200 mA, 0.6 Ω, Laird HZ0603B102R-10
Semiconductor
B1 = DF04S, 400 V, 1.5 A, SMD SDIP 4L
LED1 = LED, red, 50 mcd, 1.85 V @ 20 mA, SMD 0805
LED2 = LED, green, 50 mcd, 2.1 V @ 20 mA, SMD 0805
T1 = FZT751, PNP, 60 V, 2 W, 3 A, SMD SOT-223
IC1 = AD8552ARZ, SMD SOIC-8
IC2 = OPA2197IDR, SMD SOIC-8
IC3 = LT1021DCS8-5#PBF, SOIC-8
MOD1 = LTS 25-NP, through hole module, LEM
MOD2 = TMR 1-1211, SIP module, Traco Power
Other
K1 = Terminal block, pitch 5.08 mm, 2-way
K2,K3 = 6.35 mm TAB, Faston, 3.3 mm, TE Connectivity 42822-2
K2,K3 = Faston terminal, 6.35 mm, female, blue, 14-16 AWG, 2.5 mm2
K4,K5,K6 = Pin header, 1x2, vertical, pitch 2.54 mm
K4,K5,K6 = Pin socket, 1x2, vertical, pitch 2.54 mm
S1,S2 = Slide switch, right angle, SPDT, On-On, 100 mA, OS102011MA1QN1 C & K Components
BNC Insulated Bulkhead Socket, Panel Mount, 5-1634504-1 Greenpar/TE Connectivity
DC Power connector, receptacle, 2.1 mm, 1 A, panel mount, isolated
Banana Test Connector, 4mm, Jack, Panel Mount, 30 A, Red, Cliff Electronic Components FCR14461
Banana Test Connector, 4mm, Jack, Panel Mount, 30 A, Black, Cliff Electronic Components, FCR14460
Metal Enclosure, Hammond 1455K1201, 78x123x43 mm
45 mm 2.5 mm2 stranded wire, red
45 mm 2.5 mm2 stranded wire, black
4 x washer, Plain, Steel, Zinc Plated, M3
2 x standoff, Zinc Plated, Steel, M3, Hex Male-Female, 10 mm
Misc.
PCB 150170-1 v1.1
Discussion (4 comments)