Essential Selection Tips for MCUs in Modern System Designs
Tools
Tool support represents a key differentiator for a number of the leading MCU architectures. Although a parametric search will often reveal multiple candidates from different families of processor architecture, the degree to which the tool support fits the needs of the development team is an important mechanism for making a decision as to which to pick. It is important to take into account the skills of the developers and their experience. Engineers with in-depth knowledge of high-level languages used for larger systems will naturally gravitate toward 32-bit architectures, such as ARM, as these offer the widest range of compiler choices. Where memory and cost limitations prevail, it will make more sense to aim for 8-bit or 16-bit architectures and take into consideration some of the limitations these can impose on C code. In many cases, a wide variety of tools are available. The major 8-bit and 16-bit MCU architectures are supported by complete toolchains of compilers, debuggers and linkers, often hosted within an integrated development environment (IDE) and located in a very reasonable price bracket.Packaging
In many designs, the space needed to accommodate the MCU is an important consideration. Users frequently opt to employ an MCU solution because its high integration allows for a compact form factor to be realized. However, there will be trade-offs between the core package design and what the board-level design can support. For example, a growing number of MCUs are shipped in chip-scale packages that reduce these devices’ notional real estate as far as possible. The density of the interconnect underneath the package may challenge the PCB design, necessitating the transition to a higher-cost stackup and assembly process. Board space will also be affected by the number of supporting components that are needed and the routing choices that are available on the target PCB. In low layer-count or flexible PCB scenarios, the real estate needed around the MCU to route to I/O, clock, ground and power can increase rapidly if a large number of connections are needed. Engineers also need to consider the reliability of the device when mounted on the PCB in the context of the application’s target use. High-vibration and shock conditions may force the use of a specialized package, which in turn may entail moving to a different MCU family.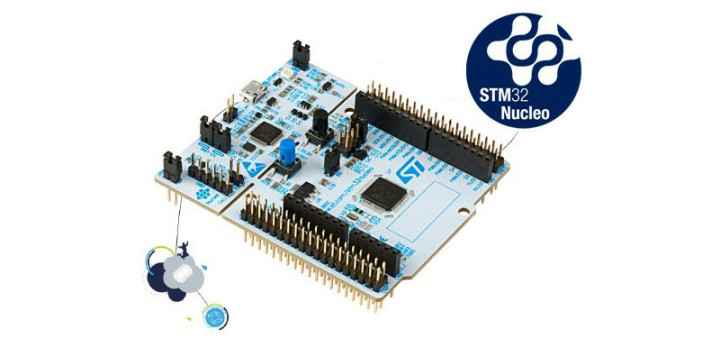
STMicroelectronics’ 511-NUCLEO-G070RB development board is based on an ARM 32-bit processor core.
Kits
Because it greatly simplifies the job of hardware design, the MCU is an almost ideal platform for situations where time-to-market is important. The comprehensive software tools that vendors now provide help ensure the final application can come together quickly. Even with these project accelerators, teams can get a further headstart by choosing an MCU that is accompanied by evaluation and development kits. These are readymade boards that carry the chosen MCU, alongside any additional I/O that a typical application will need. In addition, many of them now provide families of I/O boards that plug into the motherboard so that engineers can assemble a customized hardware solution in little more than the time it takes for the package to be delivered by the distributor. This makes it possible for teams to build a proof of concept ready to show customers simply by downloading prototype software into the evaluation system. Potentially, these evaluation kits can form the basis of early shipments while the hardware-design team works in parallel on a cost-optimized solution that will prove more attractive in the long term.About the author
Mark Patrick joined Mouser Electronics in July 2014 having previously held senior marketing roles at RS Components. Prior to RS, Mark spent 8 years at Texas Instruments in Applications Support and Technical Sales roles and holds a first class Honours Degree in Electronic Engineering from Coventry University.
Read full article
Hide full article
Discussion (0 comments)