Functional Safety and its Application to Automated Industrial Cobots
January 31, 2019
on
on
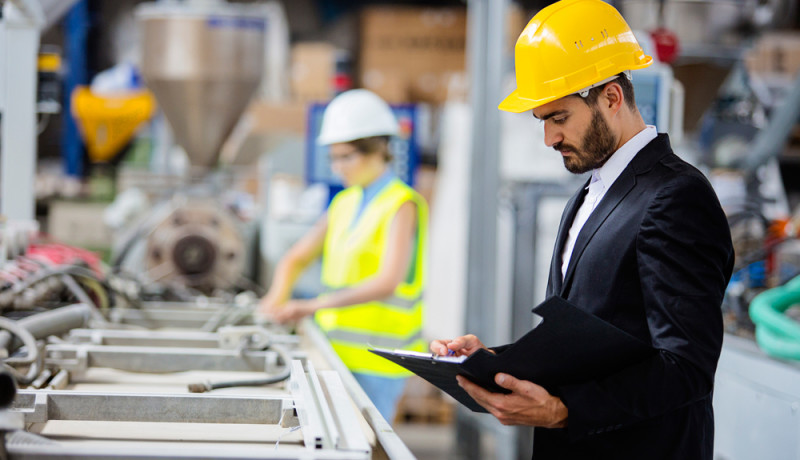
Introduction
Human Robot Collaboration (HRC) is a relatively new and emerging field in industrial robotics, offering significant flexibility and productivity enhancements by combining the power and precision of robots with the creative and problem-solving ability of humans. Whereas industrial robot systems were traditionally separated from humans to safeguard against injury, HRC necessitates a workspace that is shared between robot and human operator.
This article examines how safety relevant standards and traditional concepts of safety control are being adapted to meet the requirements of HRC systems.
Overview of Safety Standards hierarchy and framework
CE marking for a product signifies conformity with the relevant EU directive, which for industrial robots is the EU Machinery Directive 2006/42/EC. This directive defines the essential health and safety requirements (EHSRs) for machines traded in the single European market and is supported by a hierarchy of harmonised standards as illustrated in table 1, where the key standards that relate to industrial robots are listed.
Type C standards, where published in the Official EU Journal, take priority and, when a machine satisfies the objectives of the relevant harmonised standard, then “presumption of conformity” applies.
Table 1: Harmonised standards hierarchy relevant to robot safety.
Human Robot Collaboration (HRC) is a relatively new and emerging field in industrial robotics, offering significant flexibility and productivity enhancements by combining the power and precision of robots with the creative and problem-solving ability of humans. Whereas industrial robot systems were traditionally separated from humans to safeguard against injury, HRC necessitates a workspace that is shared between robot and human operator.
This article examines how safety relevant standards and traditional concepts of safety control are being adapted to meet the requirements of HRC systems.
Overview of Safety Standards hierarchy and framework
CE marking for a product signifies conformity with the relevant EU directive, which for industrial robots is the EU Machinery Directive 2006/42/EC. This directive defines the essential health and safety requirements (EHSRs) for machines traded in the single European market and is supported by a hierarchy of harmonised standards as illustrated in table 1, where the key standards that relate to industrial robots are listed.
Type C standards, where published in the Official EU Journal, take priority and, when a machine satisfies the objectives of the relevant harmonised standard, then “presumption of conformity” applies.
Standard Type | Description | Example |
A Type |
Basic safety standards giving basic concepts, principles for design, and general aspects that can be applied to all machinery. |
EN ISO 12100 (only Type A standard listed for EU Machinery Directive). |
B Type |
Generic safety standards dealing with one safety aspect or one type of safeguard that can be used across a wide range of machinery: - Type B1 standards on particular safety aspects (e.g. safety distances, surface temperature, noise); - Type B2 standards on safeguards (e.g. two-hand controls, interlocking devices, pressure sensitive devices, guards). |
EN ISO 13849-1 EN ISO 13850 EN ISO 13854 EN ISO 14118 EN ISO 14119 EN ISO 14120 EN ISO 60204 |
C Type |
Machine safety standards dealing with detailed safety requirements for a particular machine or group of machines. |
EN ISO 10218 – 1 EN ISO 10218 - 2 |
Read full article
Hide full article
Discussion (0 comments)