ICECool from IBM cools chip structure
October 14, 2017
on
on
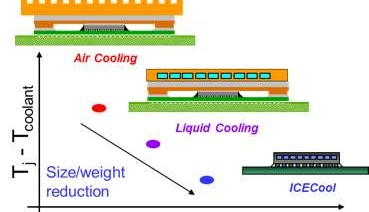
Moore's Law is proving to be quite robust despite approaching the physical limit of minimal structural width. If you were to take a close look inside a modern chip you would see structures like subminiature skyscrapers arranged in 3D stacks. This more condensed layout results in problems with heat removal, thus limiting the power and possible stacking height. To overcome this researchers from IBM have now optimized liquid cooling technology to the point that liquid can be passed directly through chip structure and thus cool more effectively.
Researchers from IBM have developed an intra-chip cooling system as a contribution to ICECool program research project by the DARPA (Defense Advanced Research Projects Agency) to find solutions for intra-chip cooling. The solution is effective at removing heat directly from the die structure.
The traditional method of taking heat away from a chip is to mount a heat sink to the chip package and remove the heat transferred to the heat sink using forced air. Hardware modders often resort to water-cooled systems when they need to remove more heat produced by an overclocked CPU. Water is pumped around the system and heat removed by a radiator and fan setup. Water is electrically conductive so it must not come into direct contact with the chip itself or any surfaces carrying electrical signals. Heat is removed from the chip package surface which puts limitations on the amount of heat which can be removed from internal 3D layers.
In the ICECool project the IBM researchers have used a cooling liquid that is not electrically conductive. This makes it possible to run the liquid directly through channels in the chip structure as shown in the diagram. Direct contact with the heat-producing semiconductor, lowers the heat resistance of the cooling path, not only delivering a lower device junction temperature but also reducing system size, weight, and power consumption. Tests carried out on IBM Power 7+ chips demonstrated junction temperature reduction by 25 ᵒC, and a fall in the chip power consumption of 7 percent compared to the same chips using conventional air cooling methods.
Researchers from IBM have developed an intra-chip cooling system as a contribution to ICECool program research project by the DARPA (Defense Advanced Research Projects Agency) to find solutions for intra-chip cooling. The solution is effective at removing heat directly from the die structure.
The traditional method of taking heat away from a chip is to mount a heat sink to the chip package and remove the heat transferred to the heat sink using forced air. Hardware modders often resort to water-cooled systems when they need to remove more heat produced by an overclocked CPU. Water is pumped around the system and heat removed by a radiator and fan setup. Water is electrically conductive so it must not come into direct contact with the chip itself or any surfaces carrying electrical signals. Heat is removed from the chip package surface which puts limitations on the amount of heat which can be removed from internal 3D layers.
In the ICECool project the IBM researchers have used a cooling liquid that is not electrically conductive. This makes it possible to run the liquid directly through channels in the chip structure as shown in the diagram. Direct contact with the heat-producing semiconductor, lowers the heat resistance of the cooling path, not only delivering a lower device junction temperature but also reducing system size, weight, and power consumption. Tests carried out on IBM Power 7+ chips demonstrated junction temperature reduction by 25 ᵒC, and a fall in the chip power consumption of 7 percent compared to the same chips using conventional air cooling methods.
Read full article
Hide full article
Discussion (0 comments)