Team up for Microchip's Dual-core dsPIC® Digital Signal Controller
July 12, 2018
on
on
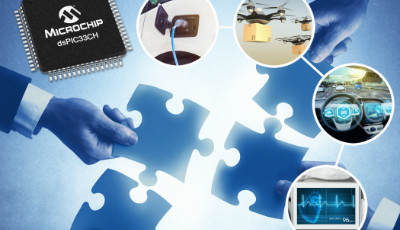
New from Microchip Technology Inc. is their Digital Signal Controller (DSC) with two PIC DSC cores in a single chip for high-end embedded control applications. The dsPIC33CH has one core that is designed to function as a Master while the other is designed as a Slave. The Slave core is useful for executing dedicated, time-critical control code while the Master core is busy running the user interface, system monitoring and communications functions, customised for the end application. The dsPIC33CH is designed specifically to facilitate independent code development for each core by separate design teams.
The dsPIC33CH family is optimised for applications requiring sophisticated algorithms, including wireless power, server power supplies, drones and automotive sensors. For example, in a digital power supply, the slave core manages the math-intensive algorithms, while the master core independently manages the PMBus™ protocol stack and provides system monitoring functions, increasing overall system performance and responsiveness. Distributing the overall workload across two DSC cores in a single device enables higher power density through higher switching frequencies, leading to smaller components.
In an automotive fan or pump, the Slave core is dedicated to managing time-critical speed and torque control while the master manages the Controller Area Network Flexible Data rate (CAN-FD) communications, system monitoring and diagnostics. The two cores work seamlessly together, enabling advanced algorithms to improve efficiency and responsiveness.
The dsPIC33CH is supported by Microchip’s MPLAB® development ecosystem including Microchip’s MPLAB® X Integrated Development Environment (IDE) and MPLAB Code Configurator.
In terms of hardware support, Microchip's offering includes:
The dsPIC33CH is available in eight package variants, from the 28-pin dsPIC33CH64MP202, to variants with 80 pins and variants as small as 5 x 5 mm. Memory sizes range from 64 to 128 KB of Flash.
For more information visit: www.microchip.com/dsPIC33CH.
The dsPIC33CH family is optimised for applications requiring sophisticated algorithms, including wireless power, server power supplies, drones and automotive sensors. For example, in a digital power supply, the slave core manages the math-intensive algorithms, while the master core independently manages the PMBus™ protocol stack and provides system monitoring functions, increasing overall system performance and responsiveness. Distributing the overall workload across two DSC cores in a single device enables higher power density through higher switching frequencies, leading to smaller components.
In an automotive fan or pump, the Slave core is dedicated to managing time-critical speed and torque control while the master manages the Controller Area Network Flexible Data rate (CAN-FD) communications, system monitoring and diagnostics. The two cores work seamlessly together, enabling advanced algorithms to improve efficiency and responsiveness.
The dsPIC33CH is supported by Microchip’s MPLAB® development ecosystem including Microchip’s MPLAB® X Integrated Development Environment (IDE) and MPLAB Code Configurator.
In terms of hardware support, Microchip's offering includes:
- dsPIC33CH Curiosity Board (DM330028 ; $34.99 each)
- dsPIC33CH Plug-in Module (PIM) for motor-control platforms ( MA330039; MCLV-2 and MCHV-2/3 versions; $25.00 each)
- dsPIC33CH PIM (MA330040; for general-purpose platforms and Explorer 16/32 development board; $25.00 each)
The dsPIC33CH is available in eight package variants, from the 28-pin dsPIC33CH64MP202, to variants with 80 pins and variants as small as 5 x 5 mm. Memory sizes range from 64 to 128 KB of Flash.
For more information visit: www.microchip.com/dsPIC33CH.
Read full article
Hide full article
Discussion (0 comments)