Rocket engine from the printer
April 01, 2019
on
on
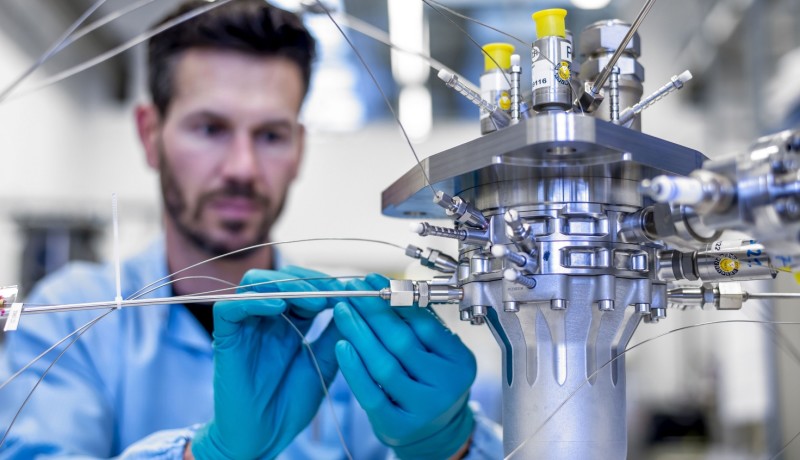
On 18 February 2019 the European space organisation ESA reached an important milestone on the (long) road towards cheaper booster rockets: on the P8 test range in the German Lampoldshausen the BERTA-rocket engine was tested successfully for the first time. By itself the test of a rocket engine is nothing special, but BERTA is something unusual.
The engine was developed in the framework for the research to future European booster rockets (Future Launcher Preparatory Programme or FLPP) from the ESA. The distribution of resources within the FLPP is driven by the German space travel centre DLR (Deutsches Zentrum für Luft- und Raumfahrt).
The usual non-perishable fuels are, however, very toxic. For this reason conventional cryogenic fuels were used for these first tests.
In the specific case of BERTA, both the injection head (made from a corrosion-resistant nickel alloy) as well as the combustion chamber (from stainless steel) were made using selective laser melting. With this, the final part is manufactured layer by layer, by the melting of a powder material on a base plate.
Using 3D-printing technology, complex structures are possible that cannot be manufactured using conventional methods. For example, BERTA contains a complex design for the cooling channels that cools the combustion chamber better. This means that the combustion chamber can be made smaller in the future, which will result in a considerable saving of materials.
It is the intention for 3D-printing technology to be used for other ESA projects, for example for the Vinci and Vulcain engines of the Ariane 6.
Source: DLR
3D printing
BERTA (the abbreviation stands for Biergoler Raumtransportantrieb) is the very first rocket engine that was made entirely using 3D-printing technology. Developed for a nominal thrust of 2.45 kN, the motor was tested continuously for a period of 560 seconds.The engine was developed in the framework for the research to future European booster rockets (Future Launcher Preparatory Programme or FLPP) from the ESA. The distribution of resources within the FLPP is driven by the German space travel centre DLR (Deutsches Zentrum für Luft- und Raumfahrt).
Fuel
BERTA has been designed for use with non-perishable fuels. Non-perishable in this context means fuels that can be stored at ambient temperatures. These engines can reliably be started multiple times and are therefore (also) suitable for longer duration missions. And this means that this engine is not only suitable for use in small and medium size rockets (which do not go higher than relatively low orbits), but also for missions that go much further.The usual non-perishable fuels are, however, very toxic. For this reason conventional cryogenic fuels were used for these first tests.
Additive production
3D-printing (also called additive production) offers various advantages for the building of rocket engines. For example, the production time can be shortened considerably. To give an example: with conventional manufacturing the combustion chambers are cast first and forged. Then the cooling channels are milled which are then galvanically covered. The typical delivery time is easily some year and a half. With additive production the complete engine can be delivered in a few weeks.In the specific case of BERTA, both the injection head (made from a corrosion-resistant nickel alloy) as well as the combustion chamber (from stainless steel) were made using selective laser melting. With this, the final part is manufactured layer by layer, by the melting of a powder material on a base plate.
Using 3D-printing technology, complex structures are possible that cannot be manufactured using conventional methods. For example, BERTA contains a complex design for the cooling channels that cools the combustion chamber better. This means that the combustion chamber can be made smaller in the future, which will result in a considerable saving of materials.
It is the intention for 3D-printing technology to be used for other ESA projects, for example for the Vinci and Vulcain engines of the Ariane 6.
Source: DLR
Read full article
Hide full article
Discussion (1 comment)