Sourcing flexible sensors for varying automation demands
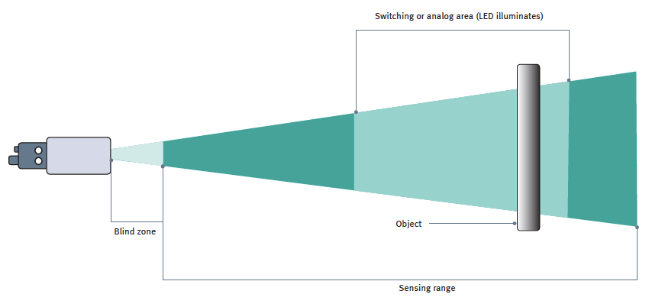
Figure 5: A diffuse mode ultrasound sensor can be configured to detect an object at a specified distance |
In some environments, the object to be detected cannot be reliably detected due to variations in the object’s colour, or due to the material it is made of. There are also challenges in detecting transparent materials, such as plastic films and glass bottles. In such situations, ultrasound sensors, either in through-beam or reflective form, are an ideal candidate. One candidate here is the UB800 series from Pepperl+Fuchs, a single head system in a short, 40mm design.
The sensors are capable of detecting items in the 50 to 800 mm range, with a dead band between 0 and 50 mm. They provide immediate indication of their status, with a green indicator showing the sensor is powered, while yellow indicates that an object is in the evaluation range. A TEACH-IN input provides a simple method for configuring the upper and lower limits of the evaluation range. The sensor provides a 20mA output for a detected object, 4mA when no object is presence, and a ramped change as objects move between the limits. The sensor is built into an IP67 rated casing.
As Industry 4.0 and more digitalisation drives more internetworked automated manufacturing systems, more and more sensors will be required to develop these platforms. With enormous variety in materials, liquids and objects being sensed, it is a challenge to determine precisely which sensor best meets the needs of the application. Suppliers are providing a wide range of solutions, with more features integrated into them. Highly visible indicators provide visual feedback on whether power has been applied, and whether an object has been detected. They are also increasingly configurable, from high-end, camera-based vision systems, down to the relatively simple distance and liquid detection sensors. Regardless of what is to be detected, it is highly likely that there is a sensing solution that matches the task’s needs.
Read full article
Hide full article
Discussion (0 comments)