Stable Temperature Sensor in Wearable-Ready Packaging
November 13, 2019
on
on
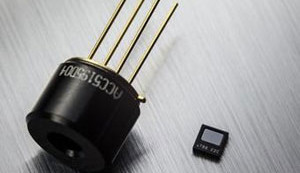
Today’s smartphones and wearable monitors, such as smartwatches and fitness bands, allow people to capture more and more data about their lives, activities, and physical condition. New services enabled by this type of data are emerging, ranging from online group fitness training to telehealth and care for the elderly.
Demand for Better Temperature Monitoring
While monitoring vital signs like your heart rate is now more user-friendly, keeping track of other signs, such as body temperature, remain rather less easy. Thermometers that remain in contact with the body are inconvenient and can be difficult to keep in place. On the other hand, non-contact FIR (far infrared) sensors can be influenced by heat radiated from sources other than the object being monitored – such as adjacent components like microprocessors or power transistors -- causing temperature measurements to be inaccurate.
To overcome this, current state-of-the-art non-contact FIR sensors are typically provided in the TO-can package. The TO-can has significant thermal mass and high thermal conductivity, which combine to mitigate the effects of rapid thermal gradients and shocks. However, the packaged sensors are physically large and heavy, and are slow to respond in a thermally dynamic environment. They are not well suited to use in devices such as consumer wristwear and could preclude temperature monitoring as a feature in emerging products, such as hearables that are designed to be worn in the ear.
Small, Stable, and Responsive
It is now possible to make much smaller FIR sensors that are also stable and accurate, leveraging a combination of MEMS (Micro Electro-Mechanical Systems) fabrication technology and advanced signal processing. The sensing element comprises a thermopile and a thin, thermally isolated membrane that has a low thermal mass. Incoming FIR radiation heats the membrane rapidly, creating a temperature differential that the thermopile can report as a temperature difference. A reference thermistor incorporated in the MEMS system enables the sensor to generate an absolute temperature measurement.
Signal processing based on careful modeling and characterization of several heat disturbance scenarios, along with sophisticated compensation algorithms, is then applied to remove unwanted thermal effects from the output of the sensor. In this way, active compensation implemented by electronics and software can effectively replace the effects achieved passively using the metal TO-can.
Demand for Better Temperature Monitoring
While monitoring vital signs like your heart rate is now more user-friendly, keeping track of other signs, such as body temperature, remain rather less easy. Thermometers that remain in contact with the body are inconvenient and can be difficult to keep in place. On the other hand, non-contact FIR (far infrared) sensors can be influenced by heat radiated from sources other than the object being monitored – such as adjacent components like microprocessors or power transistors -- causing temperature measurements to be inaccurate.
To overcome this, current state-of-the-art non-contact FIR sensors are typically provided in the TO-can package. The TO-can has significant thermal mass and high thermal conductivity, which combine to mitigate the effects of rapid thermal gradients and shocks. However, the packaged sensors are physically large and heavy, and are slow to respond in a thermally dynamic environment. They are not well suited to use in devices such as consumer wristwear and could preclude temperature monitoring as a feature in emerging products, such as hearables that are designed to be worn in the ear.
Small, Stable, and Responsive
It is now possible to make much smaller FIR sensors that are also stable and accurate, leveraging a combination of MEMS (Micro Electro-Mechanical Systems) fabrication technology and advanced signal processing. The sensing element comprises a thermopile and a thin, thermally isolated membrane that has a low thermal mass. Incoming FIR radiation heats the membrane rapidly, creating a temperature differential that the thermopile can report as a temperature difference. A reference thermistor incorporated in the MEMS system enables the sensor to generate an absolute temperature measurement.
Signal processing based on careful modeling and characterization of several heat disturbance scenarios, along with sophisticated compensation algorithms, is then applied to remove unwanted thermal effects from the output of the sensor. In this way, active compensation implemented by electronics and software can effectively replace the effects achieved passively using the metal TO-can.
Read full article
Hide full article
Discussion (0 comments)