Superior Encoder Technology Addresses the Uncompromising Industrial Landscape
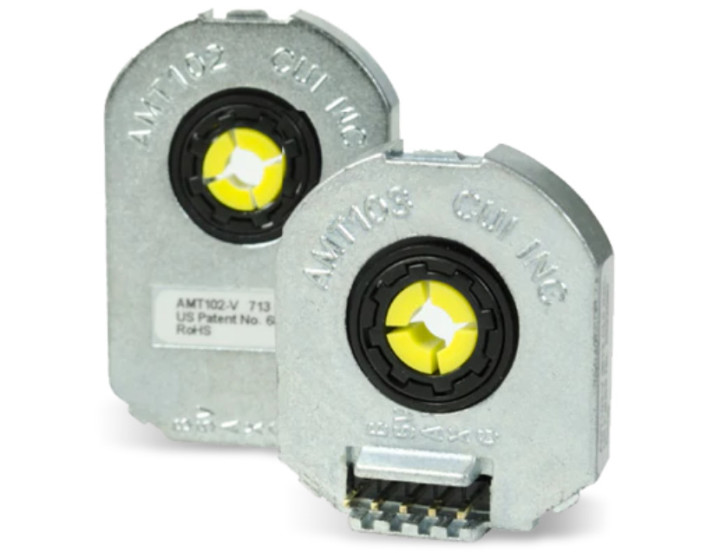
Figure 2: CUI’s AMT series of capacitive encoders.
AMT series encoders generally draw only 6mA of current even when operating at their highest resolution, whereas an optical encoder solution is likely to be an order of magnitude greater (around 50mA to 80mA) and a magnetic encoder solution even greater still (in the region of 120mA to 150mA). The component parts involved in these encoders are all long-lasting. There are no LEDs to replace, for instance. The encoder will usually outlive the motor itself, so there are no replacement costs to factor in. The longer lifespan and substantially reduced implementation time of these devices means that they present engineers with a significantly reduced cost of ownership compared to alternative solutions. Adaptive sleeves allow AMT encoders to be mounted to various shaft diameters. Consequently, there is no need to keep different encoder models in stock, thereby simplifying inventory management and keeping the associated costs down. Finally, the programmability means that, as well as accelerating the production process back in the factory, fine-tuning can be done when the encoder is in-situ.
Encoder Type | Capacitive Encoder | Optical Encoder | Magnetic Encoder |
Accuracy Level | High | High | Low |
Dirt/Dust Resilience | High | Low | High |
Operational Temperature Range | Wide | Narrow | Narrow |
Power Consumption | Low (6mA) | Medium (>50mA) | High (>120mA) |
Programmability | Yes | No | No |
EMC Immunity | High | High | High |
Magnetic Immunity | High | High | Low |
Resolution Range | Wide | Wide | Narrow |
Table 1: Comparison of different encoder technologies.
Discussion (0 comments)